The Ford Production System paved the way for most modern lean manufacturing, and the best physical embodiment of it was the Willow Run B-24 bomber production facility in WWII.
After intervention from Ford, Willow Run was able to go from producing one bomber per day to one per hour. That’s 24x their original output.
At the heart of the facility stood the “pacing clock”. This monitored what we now call takt time.
Takt time is the pulse of your operations – the rhythm and rate by which tasks and products are completed. By monitoring and setting guidelines for this single figure, Ford (and company) was able to build a facility which could produce the same as half of the entire German aircraft industry.
That’s why today we’ll be breaking down what takt time is, how to calculate it, and how it can be used in almost any system to reliably track your progress and provide an early warning system for any problems you encounter.
Let’s get started!
Takt time explained
Takt time is a measure of how long each “cycle” is in a system, usually in reference to manufacturing. Each “cycle” is the maximum amount of time that can be spent on one product or task before needing to start on the next in order to keep up with customer demand.
Although some confuse the two, takt time is not the same as “cycle time”.
Cycle time is a measure of how long a particular task (or set of tasks) takes from beginning to end. Takt time is similar, but puts the cycle time in context of what it needs to be in order to meet customer demand.
The easiest way to think about this is to see cycle time as a measure of how long something takes to complete, whereas takt time shows how long the cycle should take in order to avoid falling behind schedule.
Despite being primarily used to track production rates in manufacturing, takt time can be just as easily used to track non-physical tasks. This is because it’s a consistent measure of the rate of progress, much like keeping tabs on the heartbeat of your company (“takt” is German for “beat”, as in “rhythm”).
In order for the takt time to be accurate and applicable, however, there must be a few constants in the system being assessed. These are:
- Production must be set to meet customer demand (or an estimation thereof)
- Customer demand must be constant
- All requested products must be the same (or take the same amount of time to create)
These constants aren’t a problem for a simple system, such as one where a product is made out of one piece (eg, folding a cardboard box). However, complex systems, tasks, and products involving multiple parts can still have takt time applied and used to set an acceptable progress rate by breaking up their systems into smaller cycles.
However, I’m getting ahead of myself. For now, let’s get into how to calculate takt time…
Takt time formula
The calculation for takt time is simple, and resembles the formula for Little’s law that we here at Process Street covered a while back.
T = Ta / D
“T” represents takt time, which is the maximum time you have from starting one product or task until needing to start on the next. This doesn’t have to be a whole number, but the units you use should be the same as those for the “Ta” figure (minutes, hours, days, etc).
“Ta” shows the total available work time for the system as a whole. This figure can be confusing, but the important thing to remember when calculating it is that this should only include time when value is being added through work. It should also be expressed in the same time units as the takt time in order to avoid confusion in your calculations.
As such, Ta is calculated as follows:
Ta = Total work time for the system – time spent without adding value
Obviously, having an infinite scope for your system will render this figure unusable, and so most takt time calculations take the system as being relative to one day (or one week) of real time. Assuming we’re looking at one day of a system, with one employee working an 8-hour shift, the “total work time” would equal 8 hours, or 480 minutes.
The “time without value” figure isn’t cut-and-dry, and so is easy to miscalculate, but will include time spent on actions such as:
- Lunch breaks
- Any other work breaks
- Tasks unrelated to the system
- Set up or cool down time (eg, booting up and shutting a factory floor)
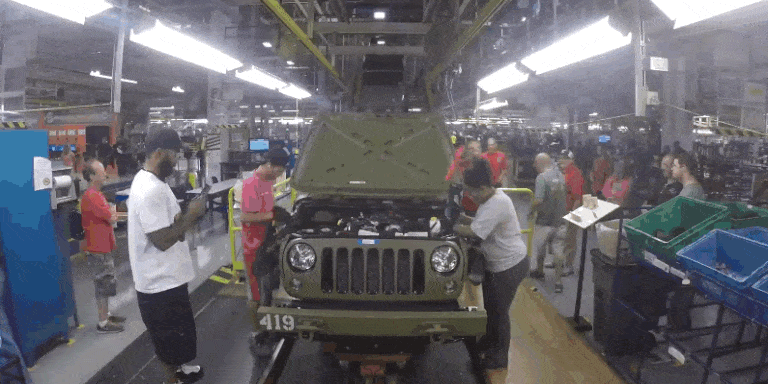
Sticking with our 480 minutes of “total work time”, we could deduct 30 minutes for a lunch break, 2 x 15 minutes for regular breaks, and (if working on a factory floor) another 2 x 15 minutes for factory set up and shut down at each end of the day.
This would leave us with:
Ta = 480 – (30+30+30) = 390 minutes of available work
Finally, “D” stands for the product or task demand of the system. This is usually stated as “customer demand” but, depending on the system you’re looking at, can be thought of as the general required output of the system.
“D” should always be expressed as a whole number (since we’re dealing with completed cycles of work).
So, in plain English, our calculation for takt time becomes:
Takt time = Available work time / product or task demand
The calculation can also be rearranged to calculate any of these three figures, assuming that the other two are known and the system requirements are met and the units are consistent.
- T = Ta / D
- D = Ta / T
- Ta = T x D
Much like Little’s law (as I’ve already explained above) the system itself doesn’t matter – the calculation is the same no matter if you’re looking at a product manufacturing system or one for completing regular tasks, such as a content promotion checklist.
What matters is that the system you’re looking at (as a whole) produces the same products or involves the same tasks every time. So long as these aspects are consistent, takt time can be used to show the available cycle time for almost any system.
The buffer zone
One last aspect to mention before diving into an example is that of the buffer zone. This is a vital, if often overlooked, aspect of takt time because of the problems in applying this to a real-world system.
“The best-laid schemes o’ mice an ‘men
Gang aft agley [Go oft awry]” – Robert Burns, To A Mouse
There will always be problems that you can’t predict. The key with making any process or calculation flexible enough to roll with these punches, rather than break at the slightest deviation, is to account for the unknown and give yourself enough leeway to maneuver in case of disaster.
In the case of takt time, the raw calculation leaves no room for error. If something goes wrong someone will need to work overtime or production will fall behind. So, while takt time shows the maximum amount of time each cycle should take, planning for this will inevitably leave you behind schedule.
This is why you need a buffer zone.
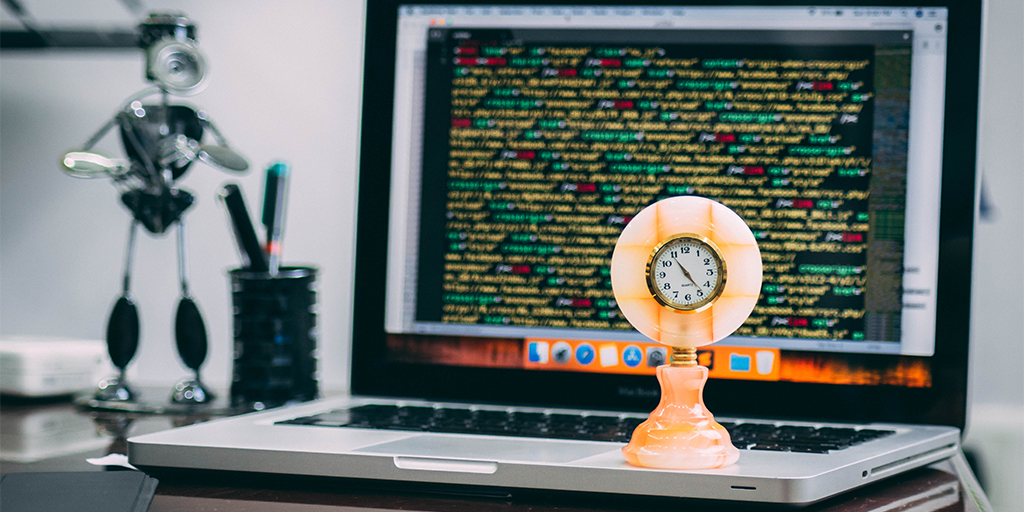
Rather than planning for your work cycles to be the same as your takt time, you should instead aim for them to be around 92-95% of that figure. The shorter your takt time, the larger your buffer should be to help ensure that you have sufficient wiggle room.
This will help you to stay on schedule and cover any potential problems with little to no downsides.
If your cycles run on schedule and don’t use your buffer, you can spend the extra time at the end of the day either doing other work or assessing your cycle for potential process improvement. If you have a few problems there’s no need to worry, as that’s what your buffer is there for.
If, however, work cycles run over even the buffer time you’ve set there are two avenues of action ahead. The first is to leave the system as it is, use up some of tomorrow’s buffer zone, and hope that the next day runs smoother. This isn’t as negligent as it may seem, as there will always be the odd day where performance is worse than usual and little can be done about it.
On the other hand, if the buffer zone is consistently (or massively) being overrun, this is a sign that something in the cycle needs to be changed in order to keep up with customer demand.
WWII, takt time, and the B-24 bomber
Now for the fun stuff – an example of takt time in action!
In January 1940, Ford was asked by the Roosevelt administration to manufacture parts for the B-24 Liberator bomber. As part of this, Charlie Sorensen (Vice-President of Production for Ford) envisioned the Willow Run bomber plant and the foundation for many modern lean manufacturing principles.
At the heart of all of this was the “pacing clock” to which they synchronized the pace of their production lines. This is what we’ve been calling “takt time”, and it allowed Willow Run to produce one Liberator per hour instead of per day.
This is a great example of a lean manufacturing process as a whole, but since we’re looking at takt time in particular, let’s go ahead and break down the individual cycles involved.
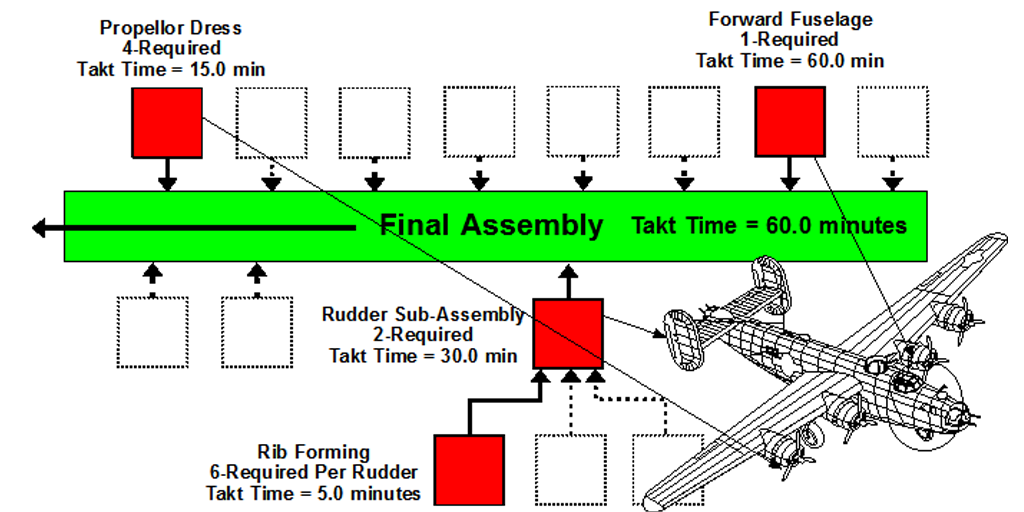
The entire production process for a Liberator bomber was intended to be an hour, meaning the takt time would be 60 minutes. To achieve this, the takt time for each component was calculated as follows:
- Four propellers per aircraft give a takt time at the propeller dress of 15 minutes
- Two rudders per aircraft give the rudder sub-assembly cycle a takt time of 30 minutes
- Each rudder requires six ribs, and with two rudders in total, the takt time for the rib forming cycle works out at 5 minutes
- Finally, one forward fuselage is needed, giving a takt time of 60 minutes
This is a great example of how useful takt time can be, as it can be used both in an overall production process and several sections of that process at the same time. The result is a target time for each part of the cycle, along with a way to measure the progress of each section and to have warning for if a certain element is taking longer than intended, thus affecting the production as a whole.
How you can use takt time
Takt time isn’t just a way to see how long each production cycle should take in order to meet customer demand. Used correctly, it can provide a steady performance metric which can give you early warning of any problems with meeting your goals and can help to pin down where your bottlenecks lie.
The base formula itself can also be turned on its head to calculate the both how long a batch order (or set of tasks) will take to complete, and even the production limits of your current operation.
Calculating available cycle time
The most common way to use the takt time formula is in calculating the maximum cycle time you need to achieve in order to keep up with demand.
This is the standard formula covered above:
- T = Ta / D
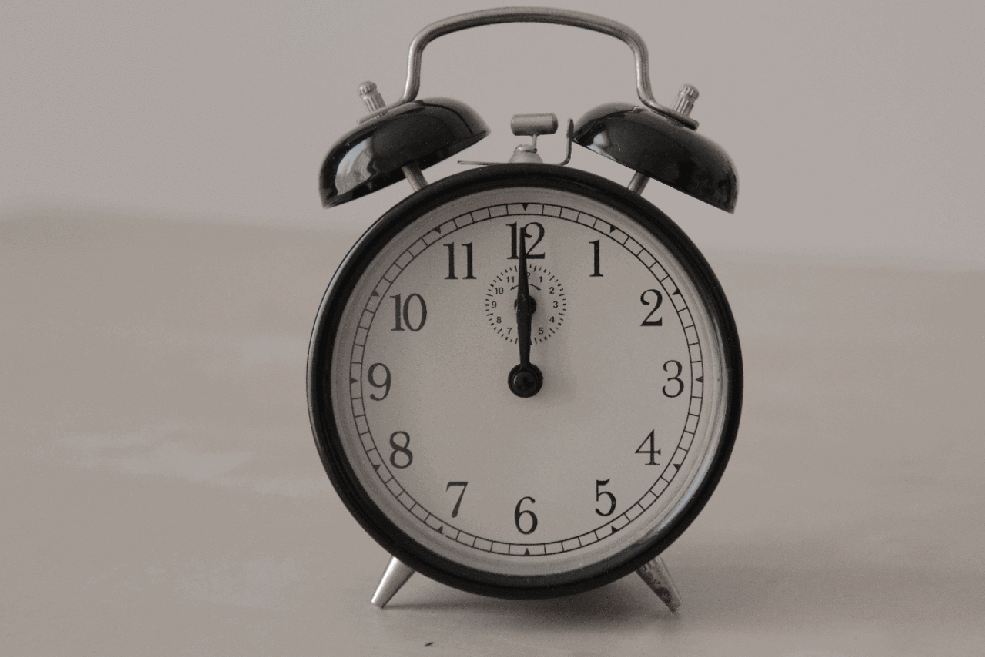
For example, if you have 400 minutes of available work time and 10 standardized products to make within that period, you know that the maximum cycle time for each product has to be 40 minutes in order to meet that goal. After accounting for buffer time, however, this will likely need to be between 37 and 38 minutes (with a buffer of 5-8%).
As with the Willow Run system, this calculation can be used to break complex production or process workflows into bite-size chunks. This allows you to set a rhythm for every procedure carried out and, when measured, allows for a consistent measure of progress over the course of your operations.
Showing total production time
The total production time an operation will take is another aspect you can calculate by changing the focus of the takt time formula to be Ta instead of T.
- Ta = T x D
While this figure is usually taken to be “available work time”, making it the focus means that you’re able to work out how long a process will need to be completed, given you know how long each cycle will take and what the product demand is.
This can be useful for large-scale operations and batch orders where many cycles (or products) are necessary in order to complete the operation in full.
For example, if you know that it takes around 30 minutes to review and process a potential hire’s job application and there are 20 applications to work through, the entire operation should be able to be completed within 600 minutes (10 hours). Knowing this will let you plan projects better in advance and plot your systems according to what your team can achieve.
Demonstrating production limits
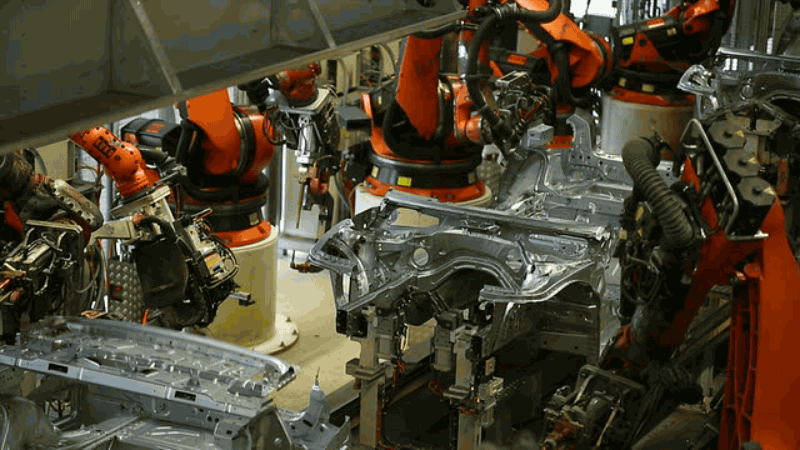
While it can be tempting, taking on more work (or orders) than you can handle will only lead to frustration on both your team and customer’s ends. Therefore, it pays to know what your maximum output is within a given time period, as this will let you give realistic estimates on when an operation will be completed.
This is done by making customer demand the focus of your takt time formula:
- D = Ta / T
Let’s say that your team (after breaks and setup time) works for 35 hours every week, and you can create your product (eg, a pair of socks) every half hour. This means that the highest level of customer demand you can handle in a given week is 70. Any orders above that will therefore need to be informed that their delivery will be going out with the following week’s order batch.
Isolating bottlenecks
The final use of takt time isn’t so much a twist on the formula, but more of a use of the figure as a measure of progress.
By splitting your production into smaller cycles (each with their own takt time figure) you can rapidly identify where problems and business bottlenecks occur, as these will be the cycles which either run consistently over schedule or perform unreliably.
In other words, if you’re having trouble with maintaining what should be a consistent output, the takt time for each cycle can highlight where your problems lie without requiring in-depth analysis to find them.
Once you know which cycles are proving problematic, this allows you to focus on that specific area as part of your continuous improvement plan.
Use takt time to measure your business’ heartbeat
Much like with other useful practices and techniques like Little’s law and business process automation, takt time becomes a true powerhouse when used with a little creativity. It’s not just a measure of manufacturing productivity after all – it can be applied to any consistent system, no matter the size or scale of the tasks involved.
Who knows? With a little ingenuity and practice, you too could follow in Ford’s footsteps and increase your output by 24x by using takt time and taking a long hard look at your business processes.
Have you used takt time in your own business? Would you care to share your own use cases? I’d love to hear from you in the comments below!
Ben Mulholland
Ben Mulholland is an Editor at Process Street, and winds down with a casual article or two on Mulholland Writing. Find him on Twitter here.