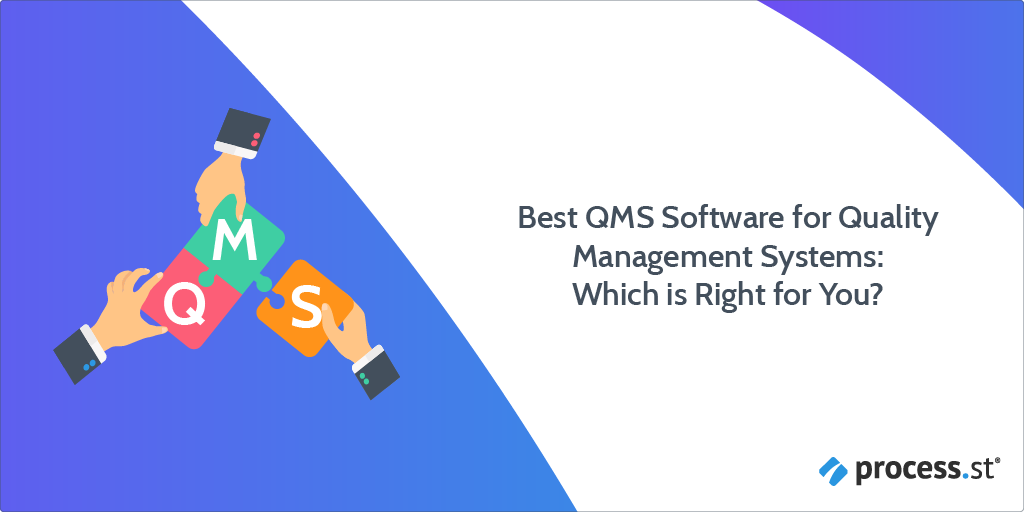
Implementing a quality management system (QMS software) is an important investment companies cannot overlook.
One Harvard Business Review study found that companies with an ISO 9001 certification have much higher rates of “corporate survival, sales, employment growth, and wage increases than a matched group of non-adopters.”
For instance, 65% of companies save $25,000 or more in costs within their first year of implementing a QMS.
Adopting a QMS software can also boost efficiency and consistency of work, increase customer satisfaction, raise product value, and reduce unnecessary costs and overall risks.
A good quality management system is all about achieving a quality-driven culture within your company, and as a result, making your product better and marketing it faster. But in order to access these benefits, it’s important that you choose the right QMS solution for you and your company.
In this Process Street article, we’ll be going over the foundation of everything you need to know before choosing your quality management system software.
We’ll be covering:
- What is a quality management system (QMS)?
- Agile QMS
- Best QMS software
- Build your agile QMS with Process Street