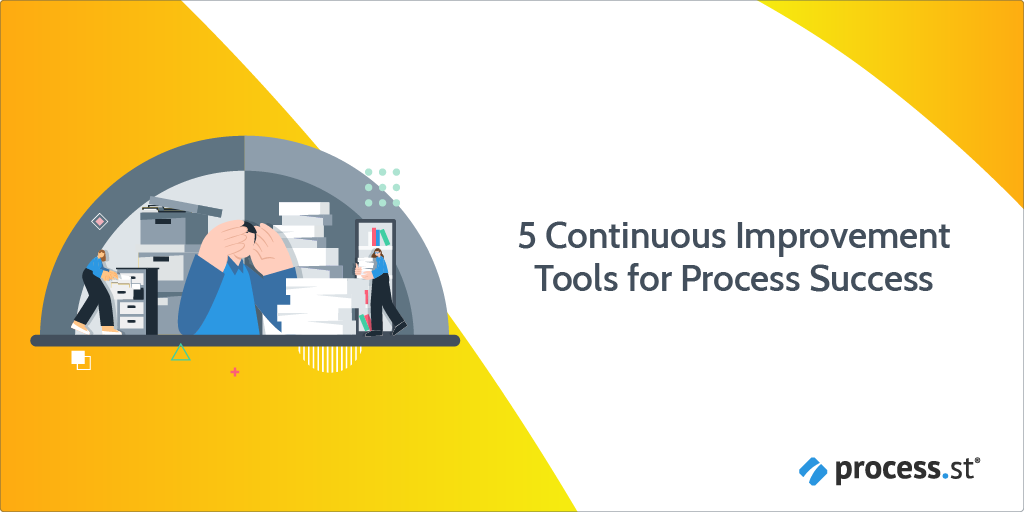
Continuous improvement tools are essential.
They’re a means of increasing productivity while eliminating errors. And they’re closely associated with lean manufacturing, particularly in streamlining processes. Every process should be continuously improved, especially in a world where checking email alone costs us 1000 hours every year.
I once used a continuous improvement tool to transform my skill level in meditation. I was amazed at how quickly a process could be made leaner and more agile. If your organization has been wondering which continuous improvement tool to use, Process Street has written this guide with you in mind.
Here’s how to transform your process for success with continuous improvement tools:
- Continuous improvement 101
- What benefits can continuous improvement bring?
- The 5 continuous improvement tools you need
Continuous improvement 101
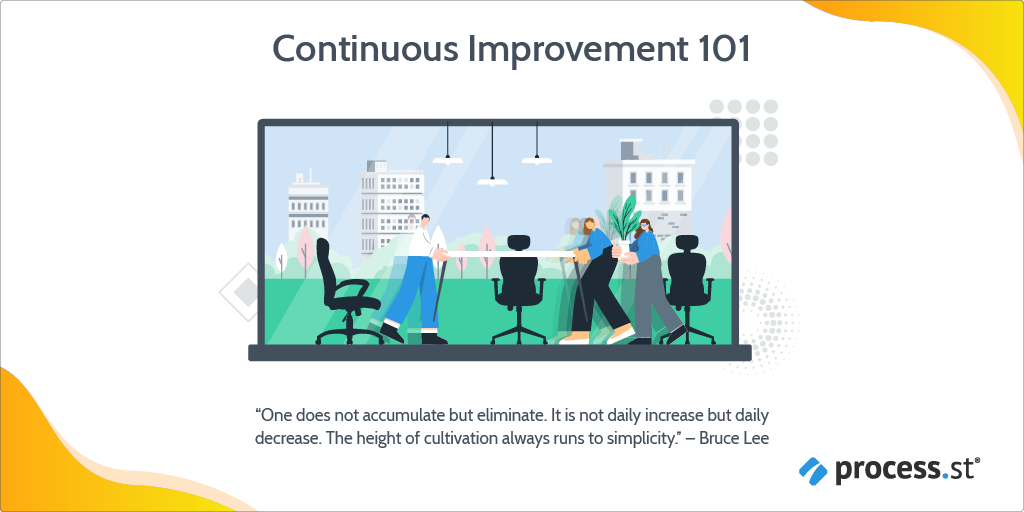
Continuous improvement is about making your work lean, agile, and effective. If you’ve improved any area of your life, you’ll know that progress has to be continuous. However, the most critical point of continuous improvement is that it must be about you and your team.
Whether your team is knowledge workers, chemical engineers, or hospital staff – continuous improvement will have a strategy to suit your needs.
The continuous improvement process
The process of continuous improvement begins with incremental enhancement. You’re on the right track if you’re thinking of minor tweaks. For example, lean production starts with fine-tuning the issue of waste. You initially make small changes to achieve that goal. Waste is anything that doesn’t add value to the process or the result.
Your journey of removing waste from a process begins with using a continuous improvement tool to create a strategy for your team. The strategy can be something as simple as upskilling.
“Lean production calls for learning far more professional skills and applying these creatively in a team setting rather than in a rigid hierarchy.“
James P. Womack and Daniel T. Jones, The Machine That Changed the World
Breakthrough improvements
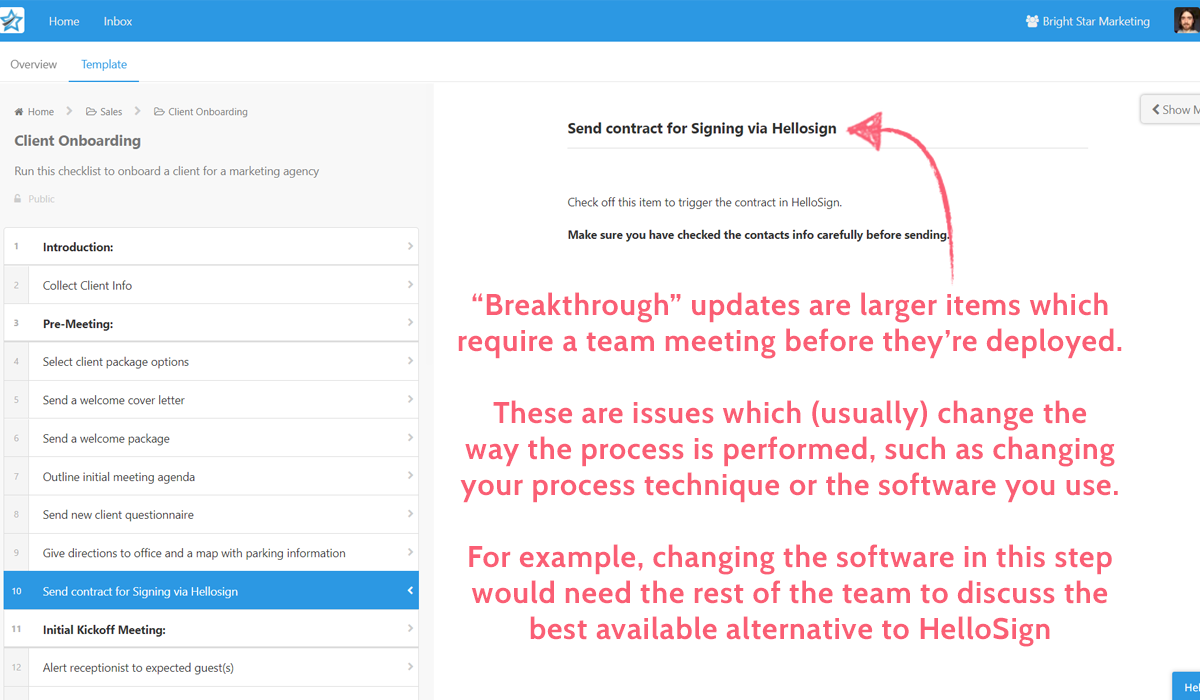
You can only see breakthrough improvements when you take your process through the lean journey.
For example, consider employee onboarding. You start by sending out job contracts and paperwork for your new hire. In the age of remote employees, mailing documents wastes essential time. One technique to remove waste would be to use an online knowledge base. You can also use digital signatures to save time on paperwork and postage.
What benefits can continuous improvement bring?
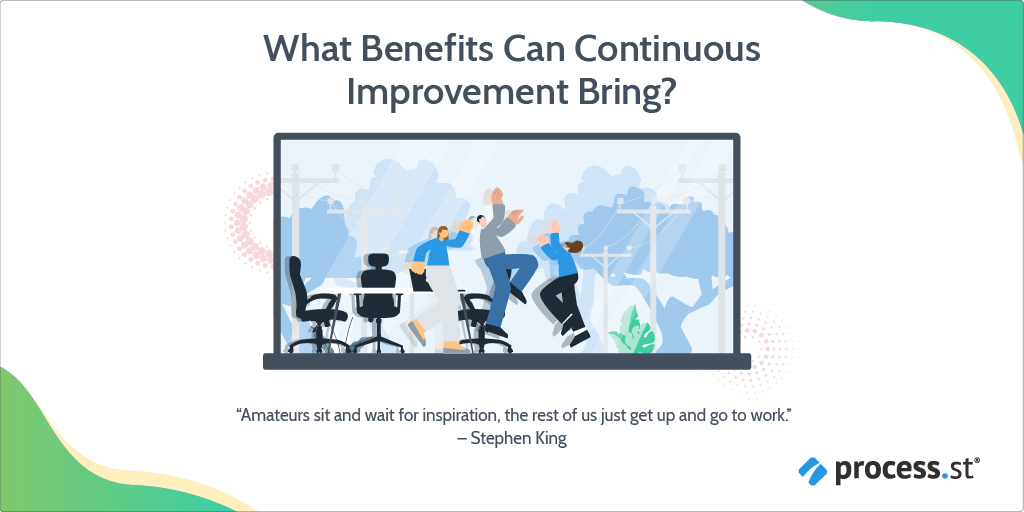
McDonald’s has enjoyed the benefits of continuous improvement for a long time. They often make their processes leaner with continuous improvement tools. McDonald’s checks every task in a process to see if it’s necessary.
When I worked for them, McDonald’s reduced the number of ketchup dispensers employees used. Their improvement meant:
- Employee time was better utilized.
- Excess kitchen inventory was reduced.
- Only one dispenser needed to be cleaned and refilled.
Continuous improvement tools save time and money
If the improvement at McDonald’s doesn’t seem substantial, have a look at the math:
Overall time saved per day: 40 minutes x 40,000 restaurants = 1,600,000 minutes saved per day.
1,600,000 minutes x 356 days a year = 9,493,333 hours saved per year.
That’s an incredible 395,555 days of labor saved annually!
You can see the benefit of making changes, however small. You may wonder if there are continuous improvement tools that allow you to optimize your processes quickly. Let’s take a look.
The 5 continuous improvement tools you need
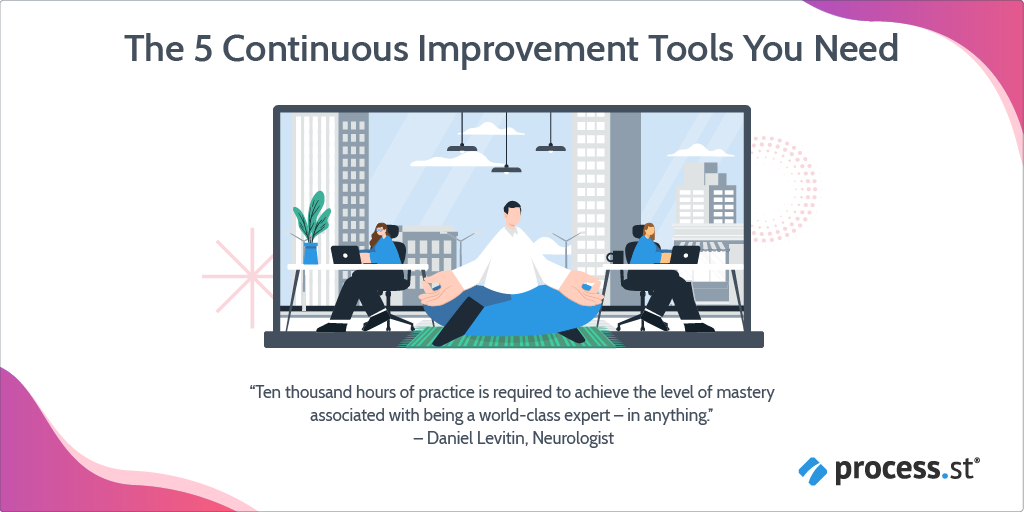
The 5 most important continuous improvement tools you need are:
These tools are all designed to improve efficiency. Please take the time to consider the strengths and weaknesses of each. Every tool has a structure you can use immediately. Using the tools will be quicker than spending hours researching process improvement methods.
1. Value stream mapping
You first need to recognize your process contributors and the tasks they are completing. A great way to do this is using value stream mapping (VSM). A tremendous continuous improvement tool, VSM can reveal where employees lose valuable time on a process.
“Taking a value stream perspective means working on the big picture, not just individual processes, and improving the whole, not just optimizing the parts.“
Mike Rother and John Shook, Learning to See
VSM involves visualizing an entire process from start to finish and looking at each task individually. You then create a diagram that outlines each task the employee performs to complete a process. VSM gives more insight into the bottlenecks a process faces.
One drawback of VSM is that you will need to identify the beginning and end of your process precisely. In a highly complex production process, that’s not easy.
“Many value streams can go on and on in both directions. For example, a value stream could include all of the activities from the time a customer selects an architect until drawings are delivered to a general contractor. Or until construction planning is complete.“
Karen Martin and Mike Osterling, Value Stream Mapping
2. Gemba walks
Gemba walks are a popular continuous improvement tool strongly linked to high-performance supply chains. The idea is that senior staff enter the Gemba. The word’s meaning is the real place: such as the factory floor, manufacturing hub, or product development area.
A Gemba walk allows senior staff to observe processes at work. Managers can decide if employees can improve their tasks and if lean manufacturing targets are achievable. This method aims to improve productivity.
“My formula for evaluating your lean efforts is therefore very simple: Examine your purpose, then your process, and then your people.“
Jim Womack, Gemba Walks
The benefits of Gemba walks are:
- The ability to interact with staff while they do their work.
- Collecting real-time data to ensure accurate reporting.
- Observing real-time work to see where errors and bottlenecks are occurring.
Management and its workforce also have the opportunity to build a closer relationship.
“An effective walk can increase credibility and build trust for all involved parties.“
Michael Bremer, How to Do a Gemba Walk: Coaching Gemba Walkers
The downside of a Gemba walk is that it does not give a cohesive or complete picture of a process. A risk is that senior managers will only hear what they want, and lower-status employees may be afraid to voice their concerns. Also, some senior staff do not allocate enough time to Gemba walks and see them only as a stroll around the estate.
3. Kanban
Kanban boards are a hugely popular agile project management tool. They allow you to visualize iterative work. Kanban lets you focus on your most important tasks first and decreases distractions. The overall effect is one of time-saving and completing work more effectively.
“You need a way to actually see the tasks you’re expected to perform so you can do the right work at the right time, and bring some clarity to the chaos.“
Tonianne DeMaria Barry and Jim Benson, Personal Kanban: Mapping Work | Navigating Life
The idea is that you have a board with three columns:
- To do
- In progress
- Done
You then create a sticky note for each project and place them in the appropriate column on your board. The benefits of kanban are prioritizing work while also seeing your progress. The process contributes to a feeling of being more organized.
“Visualizing workflow is one of Kanban’s core principles. Without engaging with workflow in a visceral manner, team members won’t recognize and resolve issues as quickly.“
Eric Brechner, Agile Project Management with Kanban
The drawbacks to kanban are that it focuses on project management, not the process. For this reason, before using kanban, it’s a good idea to ask yourself how often you have read about or watched a high-profile project fall into disarray. You may find that you prefer a tool that focuses on the process.
4. Process Street
Process Street is an efficient tool that aids continuous improvement. Process Street uses a flexible no-code editor to quickly create workflows to organize the tasks that make up your processes. Your staff can edit the workflow order at any time. Process Street lacks complication, and changes within it can be made live in no time.
The benefits of Process Street are that it shows the beginning and end of your process. This complete picture allows you to engage with the workflow. You can also clearly see any side issues affecting your processes, aiding your team or business strategy.
To see how Process Street helps to facilitate continuous improvement in your team – in under 30 seconds – take a look at the video below:
The most significant benefit of Process Street is that it focuses on the process. The methodology of the Process Street model is that process management does not get the attention it deserves. The fact is, many daily activities – that we take for granted – are made possible by systems of intricate, interlinked processes. If you like, you can try Process Street for free.
“Projects can be great for incubating an idea or figuring stuff out, but that is the end of their usefulness. Successful teams quickly transform that project into a process and shift focus to scaling and optimizing what is working.“
Vinay Patankar, CEO & Co-Founder of Process Street, The Process Manifesto
5. The five whys
The 5 Whys revolve around a question-and-answer solution as a continuous improvement tool. The 5 Whys involve asking “why” 5 times to identify a root cause. The first step to great success can come from asking why.
“Apple has successfully challenged conventional thinking within the computer industry, the small electronics industry, the music industry, the mobile phone industry and the broader entertainment industry. And the reason is simple. Apple inspires. Apple starts with Why.“
Simon Sinek, Start with Why
In a nutshell, the 5 Whys is about cause and effect. Something we humans are good at understanding.
“No other species grasps this certainly not to the extent that we do. From this discovery came organized societies, then towns and cities, and eventually the science- and technology- based civilization we enjoy today. All because we asked a simple question: Why?“
Judea Pearl, The Book of Why
I don’t love the sound of falling glass
To see an example of the 5 Whys in action, let’s look at a problem and how we can apply the methodology to it. The problem can be an ongoing or one-off event that costs time and money.
Problem: Why was last night’s store installation completed late?
- Why? We had to replace a glass cabinet.
- Why? The original cabinet fell ten feet to the ground.
- Why? The delivery driver accidentally dropped it.
- Why? He didn’t follow the procedure, and I couldn’t stop him.
- Why? Because I had to get out of the way, and I like my head on my shoulders.
Solutions: The delivery drivers working on future projects will need retraining. We could ask our staff to remove the cabinets, but we would need to ensure they are insured.
You can ask as many “whys” in the process as you like; this is also the most significant weakness the 5 Whys have. Problems are rarely that simple. They usually have many side issues that are difficult to fathom with the 5 Whys process. For example, a workflow with an ordered employee task list would show where problems are arising in a process quicker.
“Lucky is he who has been able to understand the causes of things.“
Virgil
How continuous improvement tools can help meditation
My favorite continuous improvement tool is the workflow. You might remember that I previously discussed transforming my meditation process.
At one point in my life, I had money worries and began to suffer from sleeplessness. A friend recommended using a meditation CD. Although skeptical, I agreed to try the process. The CD involved aspects of visualization. Specifically a garden full of exotic plants and palm trees. I remember, for some reason, it repeatedly mentioned stone benches.
Continuous improvement tools for the mind
For a long time, the CD wasn’t working for me. I decided to create a workflow of how I was using it. My purpose was to concentrate on improving the process. To begin, I made a list of tasks involved in using the CD. With some research, I tweaked a few tasks to make the CD work for me. These included:
- Lying down on a comfortable bed.
- Listening to the first track only.
- Practicing the meditation first thing in the morning.
Bingo. The meditation CD started to work its magic. Then I had a surprise. A rival company took over my workplace. I received a nice payout and secured the job of my dreams. The biggest surprise was when I arrived at my new apartment abroad. From the balcony, I was greeted with the sight below:
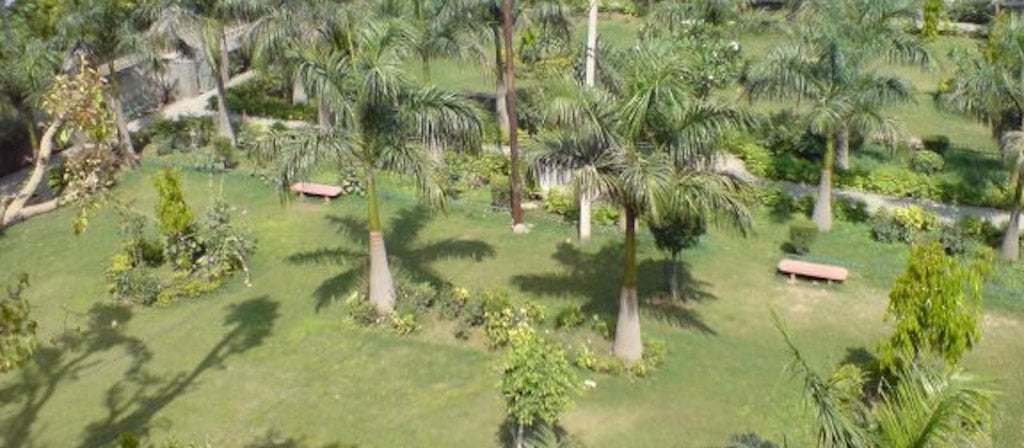
Please let us know about your experiences with continuous improvement tools. We’d like to hear if any of our five continuous improvement tools caught your interest. Please tell us in our comments box below!
Mark Jones
Mark Jones is a content writer at Process Street.