Want to lose weight? Shape up? Get fitter? Gain muscle?
If you do, I have one thing to say to you:
“If you always do what you’ve always done, you’ll always get what you’ve always got” – Henry Ford
To get better, improve, and achieve your goals, something needs to change.
But this concept doesn’t only apply to people who want to lose weight, get fit, or become stronger.
It applies to businesses too; to keep improving, businesses need to keep changing.
Businesses can typically find between 50 to 75 improvement opportunities when they go through process analysis. This can result in anywhere from a 10% to an 80% reduction in costs.
Aha! Thought that might get your attention! Interested in finding out more?
This is what you’ll learn by reading this Process Street post on process analysis:
- What is process analysis?
- How Lego and IBM nearly collapsed without process analysis
- The 4 tell-tale signs that a process needs analysis
- How to do process analysis (and how to do it well)
Ready to take the first step towards new and improved processes?
What is process analysis?
Process analysis allows businesses to assess how things are done, so they can understand where improvements can be made. It’s the first step on the road to optimizing business processes and making them as efficient and effective as possible.
All successful businesses utilize efficient and effective processes. When a company’s processes are effective and efficient, good things happen; they experience lower operational costs, higher performance levels, and improved bottom lines.
That’s why we here at Process Street created the Process for Optimizing a Process.
It takes you through all the steps involved in optimizing your processes and it will show you how and where process analysis fits into this:
Click here to access The Process for Optimizing a Process Checklist!
Or, sign up for a free trial if you’re not a Process Street user yet.
With process analysis, you’re looking to analyze the components of your existing processes so you can understand how they work, what they can do (and what they can’t), and how they’re performing. This understanding will give you a solid foundation to be able to make changes to processes that will improve your productivity, increase quality, and help you become more agile and effective.
How Lego and IBM nearly collapsed without process analysis
“Without reviewing and identifying process inhibitors and enhancements, and cutting redundancies while implementing sound process improvements, business and profits will ultimately dwindle” – LinkedIn, Impact of Poor Process on Organizations
Archaic and inefficient processes are costing companies as much as 30% of their revenue and can cause catastrophic, and sometimes even irreversible, damage.
But how do processes become ‘archaic and inefficient’?
If processes are not continuously analyzed, dissected, pulled apart, and then improved, they become slow, out-of-date, old, and wrinkly.
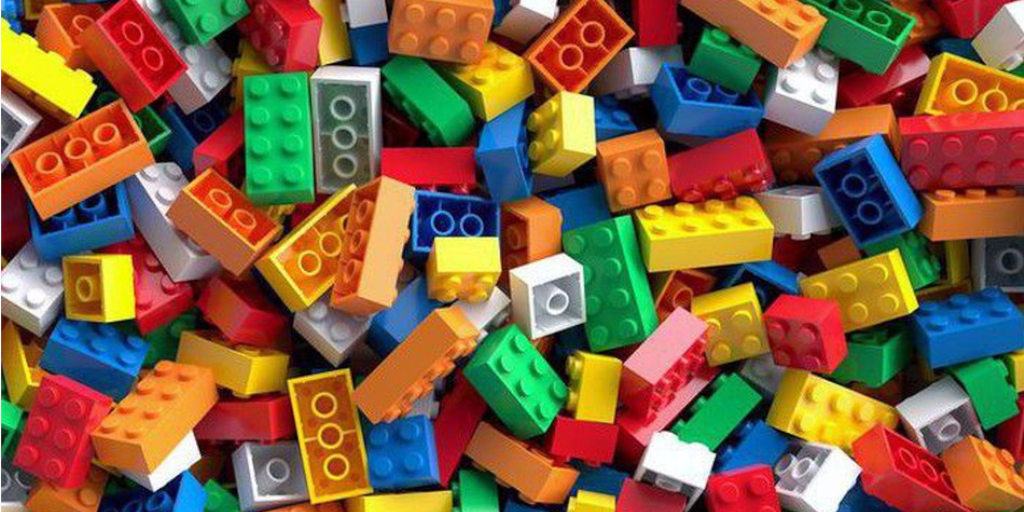
Believe it or not, Lego let their processes grow slow, old, and wrinkly and suffered a near-collapse as a result.
What saved them? Process analysis.
10 years ago, Lego came to an embarrassing conclusion. They were selling their products for less than they cost to manufacture. Ouch!
Although significant damage to profits had already been done, through process analysis, Lego found that their key direct-to-consumer and supply chain processes were highly dysfunctional, and operating in silos. These ineffective processes were the sole reason behind this shameful school-boy error.
This discovery prompted them to streamline their entire operation, and they were (thankfully) able to rebuild the company back up, brick by brick.
But it’s not only Lego that was saved by process analysis.
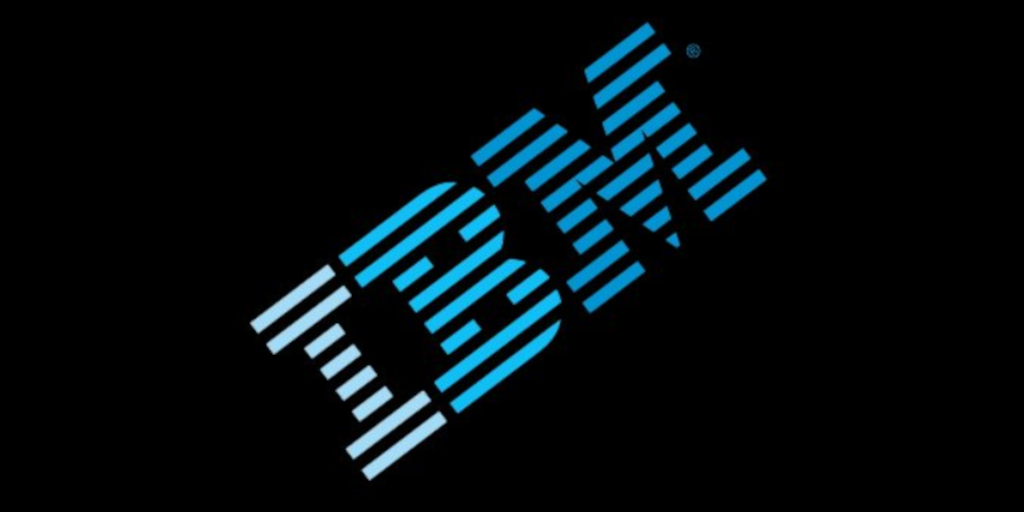
IBM also fell victim to letting the grass grow beneath their processes.
IBM has been a fixture at the top of the Fortune 500 list for over half a century. But they nearly fell from grace back in the early ’90s.
They realized, a little too late, that in just three months they’d managed to lose $45 million on inefficient day-to-day operational processes.
It took the arrival of a new CEO, Lou Gerstner, to turn the situation around.
After ruthless process analysis, he fired 100,000 people, cut inefficiencies, and loosened up the famously stodgy corporate culture. The shake-up worked and they were soon sitting comfortably, once again, at the top of the Fortune 500 list.
Although Lego and IBM used process analysis to turn things around, they were both sailing close to the wind for a while. The damage could’ve been significantly less if only they’d done it sooner.
I guess the question is then, when should companies analyze their processes?
The 4 tell-tale signs that a process needs analysis
As we’ve established, process analysis should be used to identify opportunities for improvements and locate problematic areas.
Without it:
“You could end up wasting a lot of time and effort solving the wrong problems—or putting bandages on symptoms instead of treating the problem itself” – NovaCura, How to Analyze your Business Processes
But if you do it too late, you risk losing everything, and if you do it too soon, process analysis in itself becomes inefficient and redundant.
These are the four warning signs that signify when a process needs analyzing:
- If you’re consistently seeing delays
- If your customer complaints have started to increase
- If staff and stakeholders fail to carry out a process properly
- If those using the process express concerns (and/or want to replace it with a new version)
Ok, so we know what process analysis is. We know why we need to do it, and we know when to do it.
All that’s now left to learn, is how to do it.
How to do process analysis (and how to do it well)
Process analysis is a series of steps that will help you to identify processes, discover how they work, find weaknesses, and establish ways to improve them. It allows you to measure how successful new processes are and it encourages you to keep monitoring your processes so you can keep improving.
To do it well, follow these five process analysis steps.
The 5 key steps to process analysis
Process analysis step #1: Determine the goal for the process
Take your process and establish why it needs changing. Are you looking to improve efficiency, reduce waste, or improve quality?
Process analysis step #2: Gather information about the process
Gather and document as much information about the process as possible. Get to the bottom of it, establish where it begins, where it ends, define how it works, and measure its effectiveness. Assess the value of tasks and the time they take to complete so you can uncover where the issues lie, where the opportunities are, and whether the process is meeting its key objectives.
You can do this a thousand ways. You could use flow charts, process maps, critical path methods, box plots, and other lean techniques such as value stream mapping and spaghetti diagrams.
Or you could use one of the below Process Street templates to help you gather this information:
SWOT Analysis Template
Use this template to assess risks and potential rewards while also understanding the most important factors that impact the success (or failure) of a process.
Click here to access the SWOT Analysis Template!
GAP Analysis Template
Use this template to spot the gaps and find out what information you’re missing about the process.
Click here to access the Gap Analysis Template!
Root Cause Analysis Template
Use this template to find the core reasons for a problem and see what can be done to fix it.
Click here to access the Root Cause Analysis Template!
Process analysis step #3: Establish KPIs for your new process
Find a way to measure how effective your new and improved process will be. Establish a baseline and set some key performance indicators in place so you can measure its success.
For example, if you’re looking to improve efficiency, your KPI might be to measure how long it takes to complete a process from start to finish. Measure it against your baseline so you know if your process is better or worse.
Process analysis step #4: Take action
Now you have your KPIs and you know where the issues and opportunities lie within your process, it’s time to take action!
Use the information you’ve gathered to make recommendations on what the new process should look like.
Without action, process analysis is a waste of time and money. Did you know that around 50% of all business process problems can be solved within 90 days?
Exactly! So get going!
Process analysis step #5: Monitor the process
Once your newly improved process is up and running, you need to monitor it. Keep checking that it’s delivering what you need it to and keep improving it. The more you improve a process the more efficient it gets, and the bigger the benefits will be.
I’ve given you the steps to take to analyze your processes, and I’ve given you a couple of Process Street templates to help you with it, but you’re probably wondering who Process Street is and what it has to do with these templates?
Using Process Street to analyze your processes
“Danger may be hiding in a badly executed analysis, a wrongly selected procedure or tool for a process analysis” – Management Mania, Process Analysis
To find out who Process Street is, cast your eyes over this ‘Getting started with Process Street‘ article, or if they’re a little tired after reading this post, watch this video instead:
As you can see, Process Street is super-powered checklists. It’s state-of-the-art business process management (BPM) software that allows organizations to create templates and checklists to manage their processes.
As a Process Street user, you have access to our huge template library, where you will find ready-made templates, like the ones I’ve included in this post, for absolutely anything, from standard operating procedure templates to project proposal templates.
To give you an idea, below are some additional process analysis related templates which you can grab from the template library.
Process analysis related templates
Check out these alternative analysis templates that will help you identify potential problems and find opportunities to improve your processes:
- HAZOP Analysis Process Template
- HACCP Process Template
- 5 Whys Checklist Template
- VRIO Analysis Checklist
- Ray Dalio’s Process Improvement Method
- FMEA Template: Failure Mode and Effects Analysis
Once you have your template you can then run individual checklists from it, every time you want to complete a particular process.
If the template isn’t exactly what you’re looking for, you can use these added features to turn it into the perfect process:
- Stop tasks
- Dynamic due dates
- Task permissions
- Conditional logic
- Approval tasks
- Embed widget
- Role assignments
These features not only allow you to customize your processes, they also give you the chance to create efficiencies by automating as much of the process as possible.
Speaking of which, you can connect to thousands of apps through Zapier, webhooks, or API integration to make your workflows super-automated.
Take a look at this webinar on business process automation to find out what else you can do to automate your processes.
As if that wasn’t enough, I’ve also included some extra reading for you!
Process analysis related articles
If you fancy finding out a little more about process analysis, read these related articles:
- DMAIC: The Complete Guide to Lean Six Sigma in 5 Key Steps
- How to Perform a Root Cause Analysis (Free Template)
- How to Do VRIO Properly (With Our Free VRIO Analysis Checklist!)
- What is Value Chain Analysis? How to Deliver Value & Gain a Competitive Advantage
- Gap Analysis: How to Bridge the Gap Between Performance and Potential
- SWOT Analysis Template: What, How, & Why? (Free Template)
- What is FMEA? A Practical Guide to Failure Analysis (Free Checklist)
- Workflow Analysis: Apple’s Secret Ingredient to Success
- Gemba Walk: How to Strive Forward by Taking a Step Back
- How Asking ‘Why?’ 5 Times Can Potentially Save Your Business (Free 5 Whys Template)
- The Key to Finding Your Company’s Highest Value Processes
- Experts Share 14 Ways to Reduce Time-To-Value in your Product
- How To Get Happy Tech Teams That Deliver The Highest Value First, Faster And On Time
- Finding Your Company’s Highest Value Processes
- Add value to your firm with process automation services
- The Simple Trick To Improving Your Workflow
Before I go, I want to leave you on a process analysis high.
This is another true story.
A company called Columbia Manufacturing Inc makes desks, tables, and chairs for schools in and around Massachusetts.
They needed to expand, due to an increase in demand. Sensibly, they decided to analyze their existing production processes and found they were outdated and inefficient.
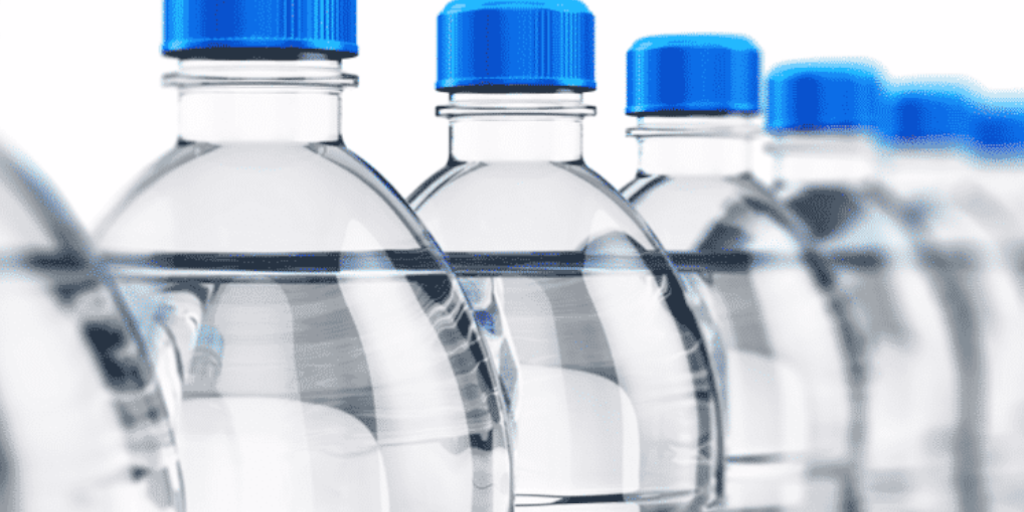
After updating and improving their production processes, they managed to eliminate the use of 147,000 gallons of water per day in their operations and, as a result, saved $3,000,000 in water and sewer fees.
How great is that?!
We’d love to hear if you use process analysis, and if you do, how it’s improved your business in the comments. Who knows? You may even get featured in an upcoming article!
Amanda Greenwood
Amanda is a content writer for Process Street. Her main mission in life is to write content that makes business processes fun, interesting, and easy to understand. Her background is in marketing and project management, so she has a wealth of experience to draw from, which adds a touch of reality and a whole heap of depth to the content she writes.