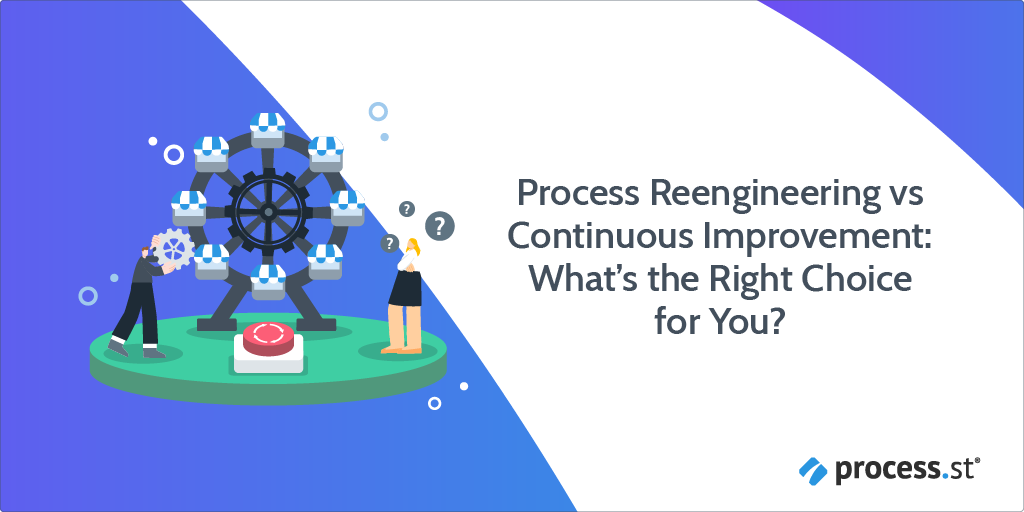
Companies need to undergo change all the time. But when do slight improvements need to be made and when is radical change a necessity? That’s where process reengineering and continuous improvement come into play.
Each is vital to the success of a company but can’t be used to handle the same set of changes. Optimizing your business operations means knowing when to make continuous improvements and when to use process reengineering efforts.
So, when’s the right time to use what?
- Diving into process reengineering
- A look at continuous improvement
- What is the difference between process reengineering and continuous improvement?
- Process reengineering vs continuous improvement: Which should you pick?
- Optimizing your processes looks different for everyone
Diving into process reengineering
Process reengineering is when core business processes undergo radical redesign. The objective of these efforts is to achieve dramatic improvements in output quality, cycle times, and productivity.
“Unplanned process reengineering is wishful thinking”
– Watts Humphrey.
Businesses start with a blank canvas when conducting process reengineering. It’s here where they rethink existing company processes to provide a more valuable output.
During process reengineering, the importance is on eliminating unproductive tasks and reducing organizational layers by:
- Using technology to enhance decision-making and data dissemination
- Redesigning functional organizations into a cross-functional team
What is an example of process reengineering?
Your organization might have a disconnected system. As a result, each customer or team member needs to go through various people and departments to solve an issue.
Everyone involved in this process is frustrated because the information is lost and people constantly need to repeat data.
Adding effective management can solve this problem. By making that change, information becomes more shareable. Overhauling the system like this requires a considerable investment in the short term, but will increase long-term efficiency.
What is the goal of process reengineering?
The objective of undergoing process reengineering is to improve overall business performance. This is done by improving customer experience, reducing costs, and outperforming competitors.
What are the stages of process reengineering?
Process reengineering (also known as process redesign) is a method of structurally changing company workflows and is made up of six stages: Idea, hypothesis, process mining, simulation, making it live, and monitorization.
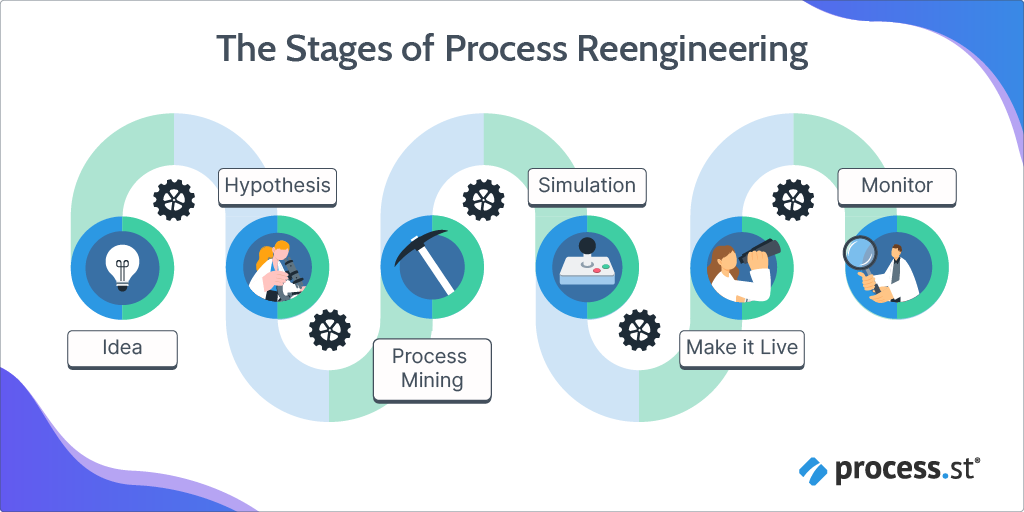
A look at continuous improvement
Also known as rapid improvement, continuous improvement is a technique used to streamline workflows.
Lean improvement is designed to enable efficient workflows that reduce wasted effort and time, which helps companies save money and resources.
“Strive for continuous improvement, instead of perfection.”
– Kim Collins.
This business strategy evaluates and revises company practices, methods, and processes. Continuous improvement is applied periodically to increase the effectiveness, accuracy, and efficiency of business processes.
This can be done by:
- Identifying an issue
- Planning possible solutions
- Testing ideas
- Implementing a specific solution
- Monitoring the results from such changes
What is a continuous improvement example?
Here’s one example of continuous improvement:
A customer success team follows a structured process when communicating with a new customer. One task includes asking various questions to understand the client’s needs.
The team typically finds that customers offer vague answers or else take a while to respond to the questions. The manager adapted this task to send out surveys that can be easily completed while providing in-depth feedback.
From this improvement in their client communication process, the team saw an increase in response rates and collected insightful feedback.
What’s the objective of continuous improvement?
Continuous improvement has two main objectives. The first is to reduce waste and the other is to streamline workflows. These two objectives work together to optimize output and reduce costs.
What are the four stages of continuous improvement?
Continuous improvement goes through four phases. These are:
- Identify
- Plan
- Implement
- Check
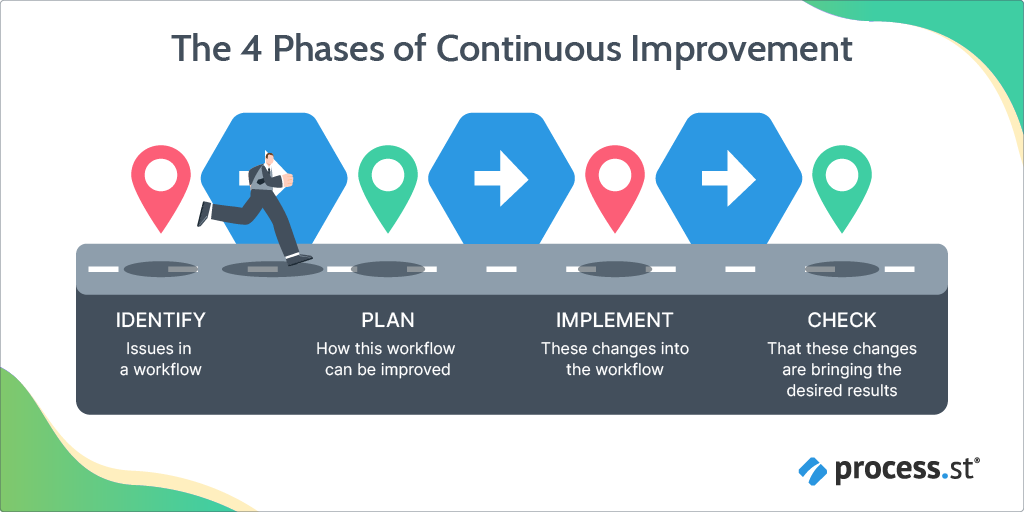
What is the difference between process reengineering and continuous improvement?
Continuous improvement and process reengineering both work to reshape existing company processes. However, process reengineering has a fundamental impact on existing processes. Instead of individual tasks, process reengineering focuses on outcomes.
Continuous improvement is the smaller changes made in a company process that improves its performance but without needing to undergo a massive change in how the workflow is run. Eliminating or rearranging the order of tasks falls under continuous improvement.
Benefits of process reengineering
With good process reengineering, your company can expect some of these benefits:
- Decreased risks
Reengineering means there is a radical replacement of a process. A complete remodel of a process helps address and correct the issues occurring from the existing procedures put in place.
During process reengineering, you make changes based on a previous process that was underperforming. This dramatically reduces the risk of process inefficiency.
- Cost-effective
Process reengineering introduces new features into an existing system. The cost of building onto this current system and making it better is less than developing a new process.
- Faster processing time
A process goes through reengineering when it’s underperforming. When the right techniques are used to improve this process through reengineering it, employees can run through the system more efficiently.
An Accenture study found a 500% improvement in process efficiency for two-thirds of businesses investing in reengineering efforts. That proves that, when done correctly, process reengineering helps improve the overall performance of a system.
- Better employee engagement
When a system is well-designed, employees are more inclined to follow it. A good process will engage employees and give them better direction over what work needs to be done.
Process reengineering allows managers to look at how their process is affecting employees and restructure it so that they can better accommodate their workforce.
For example, a process might be well-designed but the tasks may not be actionable. Employees might skip over a task they deem unimportant. If more information on how to do this task is available in the process, employees are more likely to follow through with it.
Advantages of continuous improvement,
However, if a more incremental change is called for, continuous improvement can offer these advantages:
- Easily make changes
Continuous improvement allows you to make changes to a process easily. You don’t need to undergo a complete process redesign, which saves a lot of time and resources.
Minor changes can be made to the process that doesn’t have the potential to disrupt while also increasing overall performance. You can then easily monitor this outcome and determine if your desired result was achieved.
An example might be a process that requires two approvals. One approval could be removed, as working as a bottleneck rather than adding value to the process. This makes the process run smoothly without causing any disruption.
- Affordability
In many instances, smaller businesses can’t afford to redesign their processes despite knowing that they’re running inefficiently.
Continuous improvement allows teams to make less drastic changes to their processes easily and without a costly investment. This can help them improve their processes without breaking their budget.
For larger teams, continuous improvement is also the more sensible approach. Even if they have the budget for intensive process reengineering, their existing processes might only need a few tweaks to be running more efficiently. This can also save them time and money while reaping the same results.
- Increased productivity
Continuous improvement can be done by applying small changes that have a big impact on the process’s overall performance. Productivity increases because the process is easier to work through with these improvements made, streamlining the experience. This increases the efficiency and productivity of the process.
Process reengineering vs continuous improvement: Which should you pick?
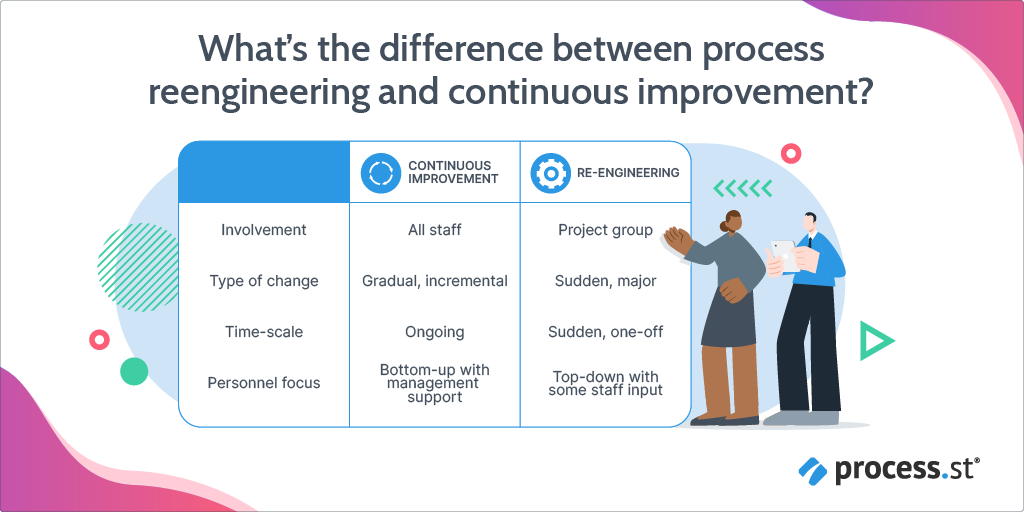
Process reengineering and continuous improvement both have a central objective – to make the process better. So, when does it come time to apply process reengineering and when would continuous improvement be a better option?
It’s important to consider your objectives before you decide if continuous improvement or process reengineering is the right choice for you:
What is your primary goal?
Understand your objectives to define whether they’re long-term or short-term. From here, you can map out what changes can be made to achieve this desired goal and see how you can implement these changes.
For example, you might have a process that takes too long to be completed. Your goal would be to reduce its processing time.
In this case, you can decide how you want to streamline your workflow. Would it be through automation? Would you need to redesign the whole process or maybe remove a few outdated tasks?
From here, you can look at:
- How many people would be affected by these changes
- How much effort would be needed to make these changes
- How long would it take to implement these changes
More people, time, and effort mean process reengineering would be your best approach.
Fewer people, time, and effort show that continuous improvement would be the best option.
The role of process management software
The common denominator between process reengineering and continuous improvement is making changes. Having a well-documented process, or better yet, using process management software, helps you make these changes easily.
Process Street allows you to make new processes from scratch or build onto your existing ones without breaking anything. New versions of the processes are reflected in real-time.
Here’s how BentoBox uses Process Street to manage its processes and scale its operations:
The data from these processes can be tracked and compared to different versions of the same process. This capability allows you to accurately determine whether these changes are providing the desired results or if other improvements can be made.
Optimizing your processes looks different for everyone
There isn’t any clear path when it comes to improving your processes.
Each process needs to be dealt with differently. Your understanding of process reengineering and continuous improvement will be the deciding factor.
That’s why it’s crucial to grasp these concepts well to ensure you’re making the right changes (with the best techniques) to your processes.
When do you think process reengineering should be used and when is continuous improvement best? Let us know in the comments.
Grace Donaldson
Grace is a content writer with a thirst for knowledge and coffee. You'll find her reading in a small café or singing at a rundown jazz bar when she's not overconsuming coffee or compartmentalizing her thoughts into a blog post.