Marie Kondo has been a bit of a Netflix phenomenon.
For those not familiar, she ventures into untidy cluttered homes and encourages people to get rid of the things they don’t need.
It’s a pretty simple base concept, in all honesty.
But the show has caught on thanks to a cutesy approach of seeing deeper meaning behind the art of decluttering.
Does this bring me joy?
… is the question Kondo forces her subjects to ask.
Sparking joy is a central theme of the Kondo approach, and this cleverly takes the workplace concept of 5s and resituates it within the home.
In this Process Street article, we’ll explore:
- What is 5S?
- What can we learn from Marie Kondo’s interpretation of 5S?
- How does 5S fit into other workplace concepts?
- How can you implement 5S into your business?
What is 5S?
5S is a Japanese framework for shaping and organizing business environments to improve output. It was originally developed alongside Just in Time manufacturing techniques.
There are 5 constituent parts to 5S:
- Seiri (Sort)
- Seiton (Set in order)
- Seiso (Shine)
- Seiketsu (Standardize)
- Shitsuke (Sustain)
Let’s explore each.
Seiri (Sort)
The first stage is the simple act of removing items from a location. This is the decluttering stage.
If something is unnecessary – as in it doesn’t add value – then it should be removed from the location.
What we want to achieve here is to reduce the amount of time you lose by rummaging around to find what you need. You should be able to identify what you need when you need it.
This has knock-on effects like making inspections easier and can also serve to reduce distractions – depending on what was present in the workplace to begin with.
Once things have been removed, you’ll also find that there is more usable space. So not only have you got rid of negative influences on the work environment, you have also opened up the opportunity to generate added value from that environment too.
In real terms, this can reduce overheads on fixed site costs as you can do more with less space while also improving safety resulting in further downstream potential savings.
Seiton (Set in order)
Seiton is all about building a good workflow.
You need to make sure that the items in the workspace are in their optimal positions.
Think about the production line in a fast food joint like a McDonald’s or a Burger King.
The burger gets cooked on the grill and the bread warmed up as it finishes cooking. They are then moved over to a unit where salad and other toppings might be added. In that workstation there will be a tub of salad, another holder for tomatoes, one for gherkins, and a rack full of sauces.
They will be arranged together in a way that one person standing at that workstation can access all of them without moving. They can apply the additions to the burger and pass it along to the next stage of the process.
You have to find out what the equivalent optimized production process is for your workspace.
Then, each item will have its place and always be found in that place. You’re looking to speed up the process and make it more efficient.
Seiso (Shine)
Seiso is all about maintaining the space. Keep it tidy and keep it clean.
A clean workspace is nicer to work in than a dirty one. It’s also more sanitary and increases safety all around.
As well as just cleaning and tidying, the Seiso stage encourages inspection. Inspection of the broader space – is everything where it should be? – and inspection of the individual items.
By routinely inspecting these items, you can care for them and reap their value for longer. You can also identify when an item needs replacing; reducing the chances of it breaking and either interrupting the workflow or, worse, causing safety concerns.
Seiketsu (Standardize)
Seiketsu concerns your process management. This is the stage where the Process Street software comes into play.
You can’t just decide that everything has a set place and needs to be cleaned regularly. You have to put systems in place to allow for that to happen.
By creating processes to manage the space you can begin to optimize and standardize those processes. This means that the best and most efficient work gets done each and every time.
Through standardization you systemize. This allows you to walk the talk.
Shitsuke (Sustain)
Shitsuke is arguably the hardest part of the cycle.
Shitsuke is often thought about as being self-discipline; make sure the processes you’ve defined are actually adhered to.
But it’s actually a little more than that.
Shitsuke translates more accurately to “do without being told”.
In this sense, Shitsuke is about workers taking responsibility themselves for the completion of these tasks. It’s about taking the regular management of these tasks away from the higher-ups, so they can focus on other areas. But it’s also about giving the workers a sense of ownership and pride over their space.
It’s easy to feel disenfranchised in a workplace. One thing which can help fight that is a sense of ownership. Simply being responsible for your own space can give a sense of groundedness; resulting in a well-maintained workplace, but also in general workplace happiness and productivity.
This ties in with broader Japanese management ideals and ethe – trust in your workers and empower them to deliver you success.
What can we learn from Marie Kondo’s interpretation of 5S?
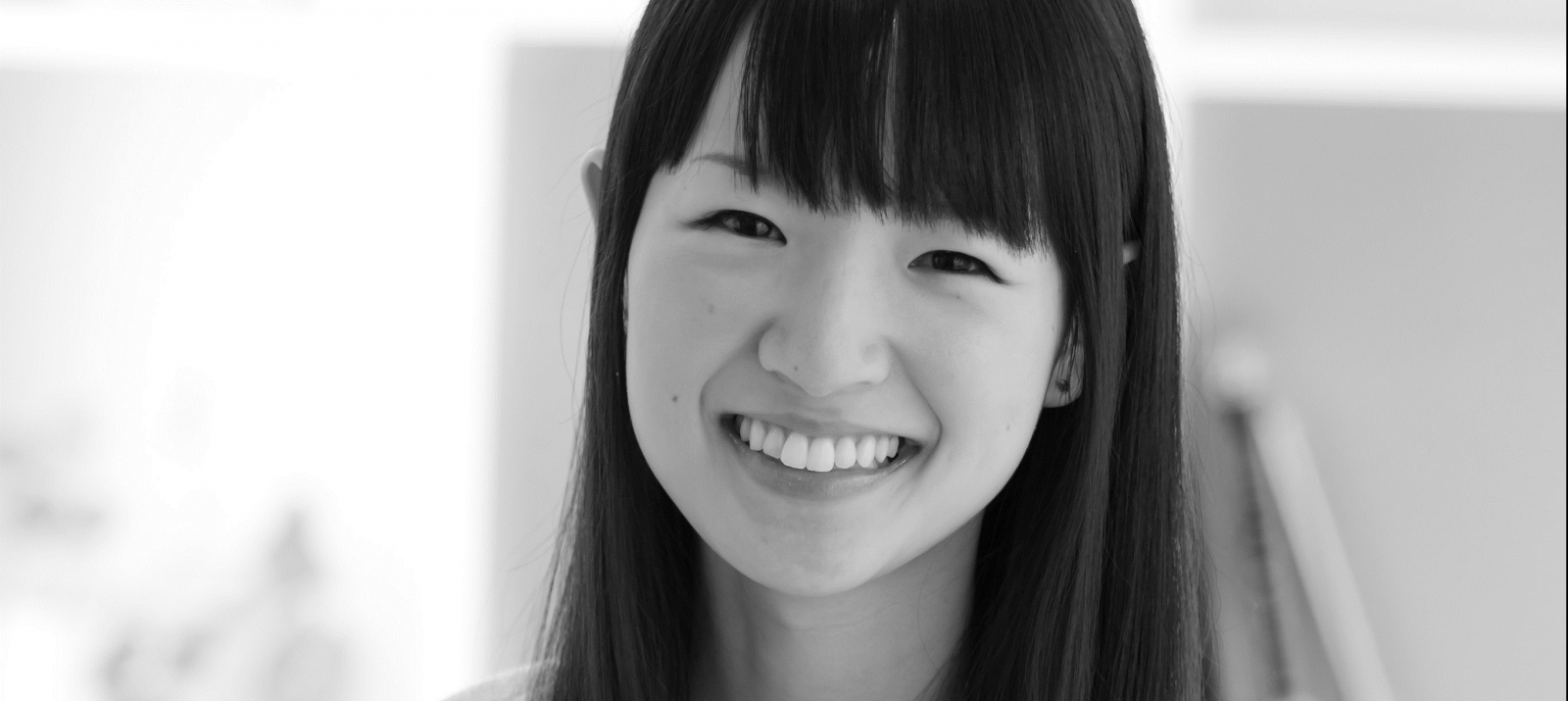
The first thing to note is that Marie Kondo uses 5S in a pretty traditional way.
She follows the methodology clearly and systematically, so understanding 5S takes us some way to understanding her reinterpretation.
Where Kondo’s approach differs is in determining what should stay or what should go.
For her, it is about sparking joy.
This is described as a kind of ephemeral feeling; a non-rational response to an object or item which should give you a sense of how important it really is to you.
You can see a super quick overview of how Kondo believes we should determine joy in this video below:
Or, if you’re really interested in interpreting her work to a deeper level, I recommend watching this extended video of her talk at SXSW:
In that video, she takes the concept further and applies it to a broader range of use cases; many where you might not expect the concept to be applied.
Her concept of sparking joy appears to be rooted in an analysis of the purpose of the home.
A home must be both functional and comforting. You need a well-organized home in order to live without too many complications, and a solid system helps unleash that.
However, a home has greater value than just being a functional machine. A home is an extension of oneself, where you’ve gathered memories and items over time. It’s a place where you want to relax and find happiness after a long day. It’s somewhere you want to bring up children and give them happiness, comfort, and security too.
As a result, she identifies joy as the productive unit of the home machine. A home should produce joy. Simplicity and sentimentality together.
This idea of joy as expressed by Kondo is a repurposing or reworking of the idea of value.
The idea of value is what drives businesses and other organizations forward. It is the output they produce reflected at each stage of the production process and its supporting features.
5S, then, performs in much the same way as Marie Kondo’s methodology but instead of picking up an object, holding it to your chest, and sensing for joy, you must identify physical (and possibly non-physical) aspects of a workplace and measure whether they add value.
How does 5S fit into other workplace concepts?
5S is a small part of a larger school of Japanese thought.
It has similarities to other Western concepts, such as the visual factory; a concept which existed independently of 5S but has now largely merged with it as part of environment design within lean manufacturing.
What I’ll do here, is pull out three specific workplace concepts with which 5S is tightly related.
These are useful concepts to understand and think about if you want to implement 5S into your business.
Just in Time (JIT) and 5S
Just in Time refers to process innovation for reducing waste.
The idea is that what you produce meets the demand exactly and doesn’t create any unnecessary excess.
To use JIT, you’ll need to stop yourself over-producing goods, using up too much storage space, and will need to accurately understand your demand in order to deliver these kinds of goals.
It could be good to think of JIT as being a manufacturing goal. It’s very difficult for a company to deliver a fully Just in Time system, but striving to is all about reducing waste.
You could also look at One Piece Flow as a related concept: How One Piece Flow Can Reduce Your Operations Time by 96%
But what waste are you trying to reduce in order to reach the goal of JIT? That brings us to Muda.
Muda and 5S
Muda basically just translates as waste. But it is a specific conception of waste.
There are a number of modern reinterpretations of Muda where the idea has one or two more elements tacked onto the end of it.
You could think about the waste of employee talents as another variable, or environmental waste in the form of pollution or unrecyclable outputs.
Generally speaking, the original conception of Muda contains these following constituent parts:
- Waste of overproduction (largest waste)
- Waste of time on hand (waiting)
- Waste of transportation
- Waste of processing itself
- Waste of stock at hand
- Waste of movement
- Waste of making defective products
Your goal is to identify each in your business and begin efforts to reduce them. Your efforts to reduce them may be aligned with the ultimate goal of being able to provide a functional Just in Time system.
But all this waste can’t simply be eliminated overnight.
It also may be that the waste is tied up with your production system in a way that it can’t simply be removed or reduced. This requires the adaption of your system over time to begin to meet these goals.
Steady and systematic improvement over time allows you to carefully get rid of the waste in your operations. Which brings us to Kaizen.
Kaizen and 5S
Kaizen is pretty much exactly what was described above. It translates essentially to “continuous improvement”.
You identify something to improve. You find ways to improve it. You improve it. You measure it. And you look for ways to improve it again.
It’s that simple.
There are, of course, a whole bunch of ways you can approach continuous improvement.
You could go super technical and look at Six Sigma concepts like:
Or you could take a more generalist approach and adopt a PDSA style route – something I explained at length in our article on The Deming Cycle.
For improving a whole business rather than simply a single process you could look at things like:
These are really all just subtly different approaches to continually identifying things to improve and then getting that done.
5S is a part of Kaizen and Kaizen is a part of 5S.
How can you implement 5S into your business?
Let’s go through each of the 5 S’s one by one and look at how you can implement them and make 5S work as a system for you.
In the following actionable pieces of advice, we’ll look at your traditional shop-floor systems but also touch on some of the ways in which 5S can impact on other workspaces, even digital ones.
Sort your space
- Evaluate the current area
- Identify items which do not add value
- Create a middle space using red tape as a holding cell for items
- Remove all items which do not add value
- Any items which cannot immediately be removed go into the holding cell
For a digital company, think about how many different pieces of software you’re asking your team to use. Think about how easy or hard it is to manage the various tasks spread between them. Where are you centralizing information and how is it stored?
Put everything where it should be
- Figure out the optimal layout for the remaining items
- Make the arrangement as good as possible but do not waste time through over-planning at this stage
- Ensure everything is easy to reach and that frequently used items are closest
- Use labels and draw outlines in marker pen to define exactly what should live where
- Discuss the outlines and locations with your team for collaborative feedback
If you’re a digital team, you might want to make sure that your folder systems and in order and correctly labelled. Simple things like clear and accurate labelling can go a long way. Do not use abbreviations if you think someone from the street wouldn’t understand them.
Make the place shine
- Clean everything
- Make sure cleaning supplies also have their space and can be easily accessed
- Decide to clean the space daily or at another appropriate interval for your industry
- Tell people that they are responsible for keeping their space clean
It’s important to note that we’re not asking your highly expensive engineering team to spend time out of their day being paid huge amounts per hour to mop. But if they cover a desk in shavings or even just spill a coffee, then someone on the team needs to take responsibility for that. You can still have an external cleaning team come in to perform the regular cleaning tasks also. If the workspace becomes a mess by 9:30 am, it should not stay a mess until the cleaners arrive at 6 pm. The team have to take responsibility.
Standardize your processes
- Make a Process Street account
- Record your processes for maintaining your space and inspecting your items
- Assign those processes to the relevant individuals
- Schedule those processes daily, weekly, or monthly depending on need
I’m joking. I wouldn’t sell that hard.
Or would I?
This is literally what Process Street was designed for and what it does best; managing recurring workflows so that they are actionable and accountable.
I’m not apologizing for it. If you want to standardize your processes then you have to take the necessary actions to do so. Using Process Street is your action. Don’t @ me.
Be self-disciplined and get it done
- Make sure the team know they are collectively responsible
- Break up tasks and hand out individual responsibilities
- Check your Process Street processes are assigned to the correct individuals
- Try to build notifications for those individuals on the devices or platforms they use.
That last one is an important takeaway, in my opinion. It’s one which people overlook so often. With Zapier, you can connect platforms together so that they can talk to each other. If your team use Slack every day, then build notifications into Slack. You could integrate Process Street and Slack for example. Or if you’re an email based team, turn on your Process Street email notifications. Or just use Zapier to trigger text messages to your team when their tasks are due, if that’s what’s right for your business.
Another option is to use some of the other features of tools like Process Street. If you build your cleaning, maintenance, and inspections into your broader processes, then you can use features like Stop Tasks to make sure the whole process can’t be completed until that task has been.
Implement 5S for a cleaner, safer, more productive work environment
Even if you don’t go as far as implementing a Six Sigma level of keeping your workspace clean and tidy, it is really worth your while taking the basic steps mentioned in this article.
If you’re not sure whether to bother or not, watch an episode of Marie Kondo where she sorts out someone’s home.
You’ll see the elation and relief on the faces of the people she’s helping out.
She has simplified their life, not just their room.
There is significant benefit to be had by de-cluttering a workspace, and it’s not just about giving you joy – it’s about making your business better.
Heed Kondo’s advice and our advice and implement 5S to spark a bit more joy in your operations.
Have you implemented 5S in your business before? Or have you worked in any companies which were an incredible mess? Let us know about your experiences in the comments below!
Adam Henshall
I manage the content for Process Street and dabble in other projects inc language exchange app Idyoma on the side. Living in Sevilla in the south of Spain, my current hobby is learning Spanish! @adam_h_h on Twitter. Subscribe to my email newsletter here on Substack: Trust The Process. Or come join the conversation on Reddit at r/ProcessManagement.