Finding ways to improve processes within your organization can be tough.
There always seems to be so many things to measure and so many variables to consider.
Where do you start? How do you determine what’s good? Who takes responsibility for improvement?
Fortunately, you don’t have to go in blind.
There are loads of approaches you can take to process improvement, but one of the key techniques used by some of the world’s top companies is Six Sigma.
The Six Sigma school of thought is all about finding the right focus and tightening up processes around that goal. The end result should be the reduction of defects from a process. This saves resources, time, effort, and most of all money!
In this Process Street article, we’re going to give you an intro into Six Sigma while linking off to resources for you to explore deeper.
We’ll investigate the key Six Sigma principles which can shape and direct process improvement in your business.
The core Six Sigma principles
The 7 key Six Sigma principles we’ll cover are:
- Always focus on the customer
- Understand how work really happens
- Make your processes flow smoothly
- Reduce waste and concentrate on value
- Stop defects through removing variation
- Get buy-in from the team through collaboration
- Make your efforts systematic and scientific
You could categorize these as lean Six Sigma if you want to as well.
Given the evolving nature of the different schools of business process improvement, there will always likely be some disagreement over what the specific principles are.
For this reason, I feel it’s important to include the various competing principles even if some other lists might look at only 5 or 6 principles.
What is Six Sigma?
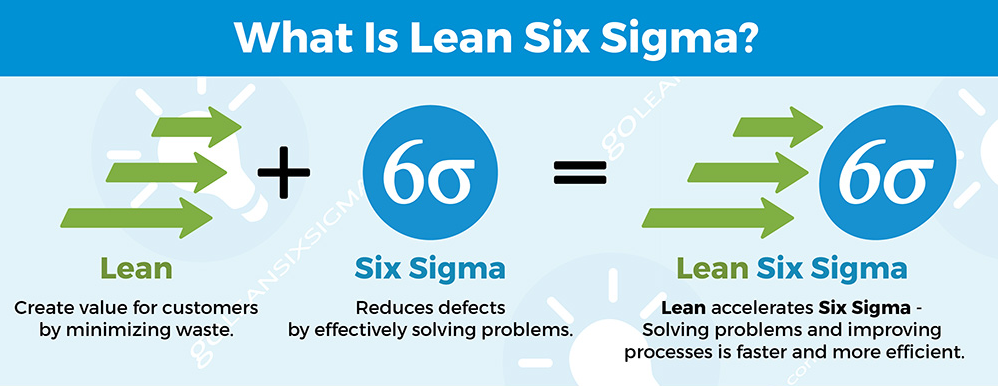
It’s fine to start talking about Six Sigma principles before actually defining Six Sigma and what it means, because I feel the principles themselves probably tell us more about how Six Sigma operates in practice as part of a process improvement effort undertaken in a holistic way.
Within the scope of this article we’ll be looking at a Lean Six Sigma style approach, but the term Six Sigma is a technical term with a specific meaning…
Managers use Six Sigma to find and reduce defects
Imagine you run a factory and on your assembly line you pump out loads of units of the same product. You want that product to match its design specifications on every iteration. This is what the customer wants and you want to make them happy.
However, in any large assembly line process you’ll end up with some defects. Some products may come out slightly wrong or very wrong. These are then products that won’t make the customer happy.
Ideally, you have a quality assurance team or process stage which identifies these defects and stops them being sent to the customer. In this scenario, the defects are simply a kind of industrial waste. Producing them has wasted time, money, and resources which could have produced a functioning product.
Yet, not every product which is defective will be caught as being defective. Maybe it’s because your quality assurance system is not very effective, or maybe it’s because the defect is quite slight, internal, or one which will only appear after a short bout of use.
Defects create waste which is bad for business
In this scenario, you’ve not only wasted time, money, and resources, but you’ve also disappointed a customer and wasted all the efforts to take that product from the end of the production line to the customer. If your product is the kind which relies on customer loyalty – something they buy regularly – then this is a pretty terrible situation to be in, as a customer may move to a competing brand.
Both of these scenarios are the fault of defects. The important thing about Six Sigma is that it takes the perspective that defects are the fault of processes.
Therefore, in Six Sigma we try to calculate how many defects we produce per million units. This gives us an objective measure to judge our process improvement efforts against.
For a real life example, we can look to the Radiotehnika factory in Latvia at the end of the USSR. A reporter from the Seattle Times went over to find out the state their industrial output:
I stopped to ask a question of a line supervisor. I asked what the rejection rate was for these parts. I asked the question several times, because I couldn’t believe the answer. The supervisor couldn’t be telling me it was 95 percent. Products made in the Soviet Union don’t have a good reputation, but 95 percent seemed a bit much.
Ninety-five out of every 100 parts made were rejected. This was a sign of waste, inefficiency, and failure.
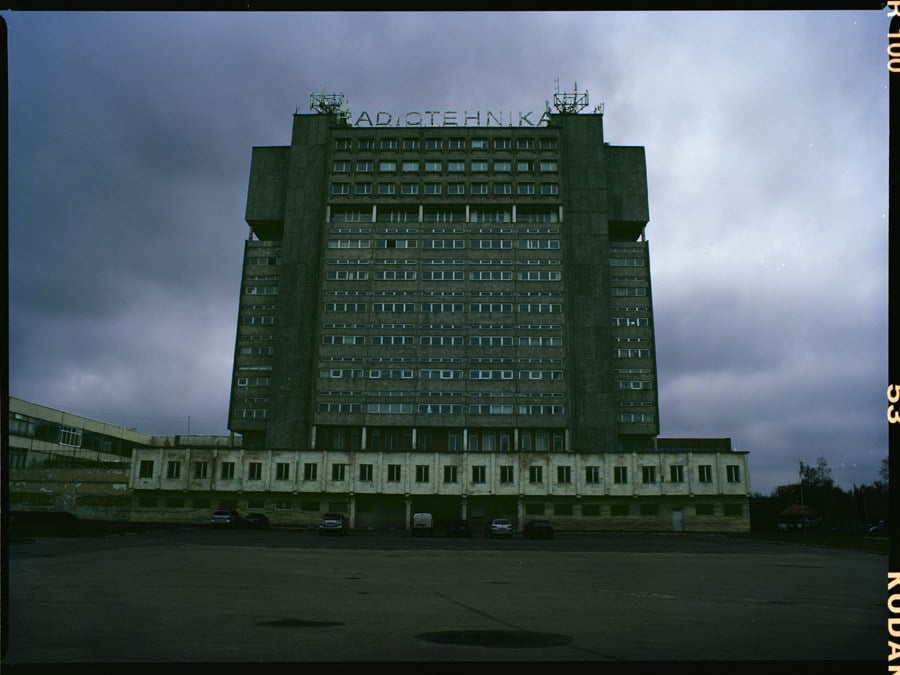
A sigma tells us how many defects we have to deal with
An improved process should reduce the number of defects per million. How many defects you produce per million is broken down into categories, or sigmas.
The idea of sigmas comes from standard deviation, and we want to reduce deviation as much as possible. At sigma number 1, most products are defective and this is a really terrible position to be in.
The realistic scenario for many companies is that their process is operating at a sigma of 3 or 4, if it’s good. A sigma of 3 means 93.32% or above of products are non-defective. A sigma of 4 means 99.38% of products are non-defective.
They both look like good numbers, but when operating at scale that 6% difference between the two has massive results. A sigma of 3 leads to 66,800 defects per million. While a sigma of 4 results in 6,210 defects per million. That’s a 60,000 unit difference!
The goal is to reach the blessed Six Sigma category where you’re only experiencing 3.4 defects per million units.
You can check out the full list of sigma breakdowns in this handy image below:
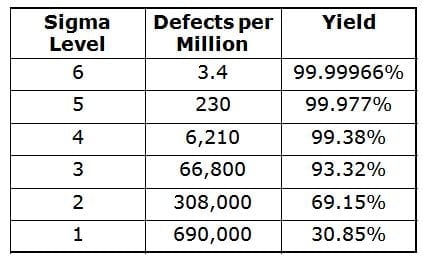
So, that’s what Six Sigma is.
But what are the principles which get us there, and how do they work?
Let’s go through each one by one to find out a little more about how they work and how we can implement them. With each principle we’ll feature an article which we think can provide some good extra background on the topic.
Always focus on the customer
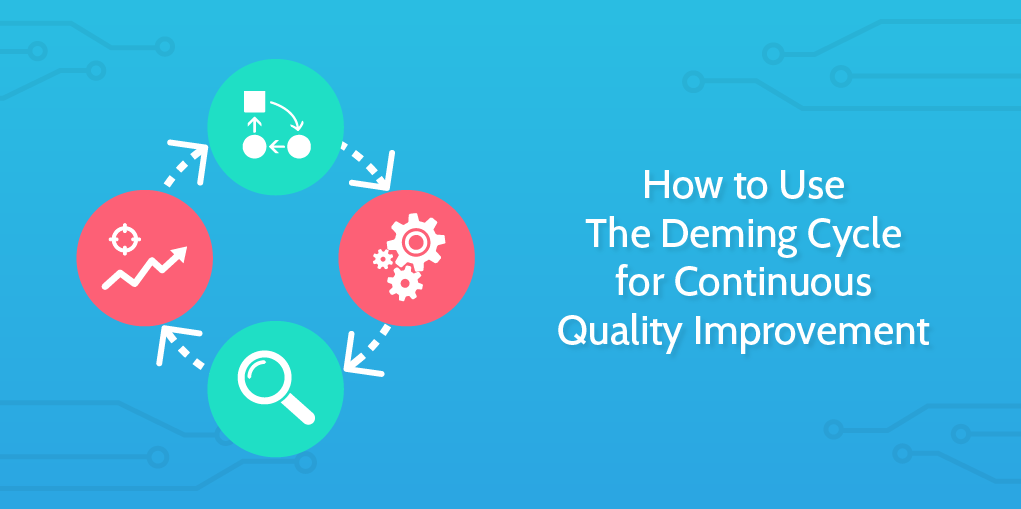
When taking a good approach to Six Sigma it’s worth pausing a moment to reflect on what you’re doing and why.
Process improvement for one single process is always going to have a limited scope with limited considerations. But we’re not talking about tinkering with a single process.
We’re talking about using the core principles of Six Sigma to drive your business forward.
We’re talking about a holistic use of Six Sigma to better your whole business, not one component of it.
This could be argued, but the key thing we want to do is improve the value for the customer and our ability to deliver that value.
There is little point optimizing the production process of a product which no one wants to buy.
The Deming Cycle idea of quality captures this well.
In fact, in my article on the Deming Cycle I specifically describe why it is important to mesh the kind of ethos present in Deming’s work with other process improvement methodologies like Six Sigma.
A clear concept of what constitutes quality in your business shapes how you improve products and processes. You need to understand what your value is and how that can be improved.
Value for the customer is a good external idea which can shape your activities.
When we come to assess waste in the production process, for example, we’re looking to cut out activities which do not contribute value. That’s how we come to understand what is wasteful and what is not. If you haven’t assessed what your value truly is then you’re unable to effectively determine what’s wasteful – therefore, incapable of making the necessary improvements.
Process improvements are a means to an end, not the end itself. Deming does a great job of elucidating why that is.
Understand how work really happens
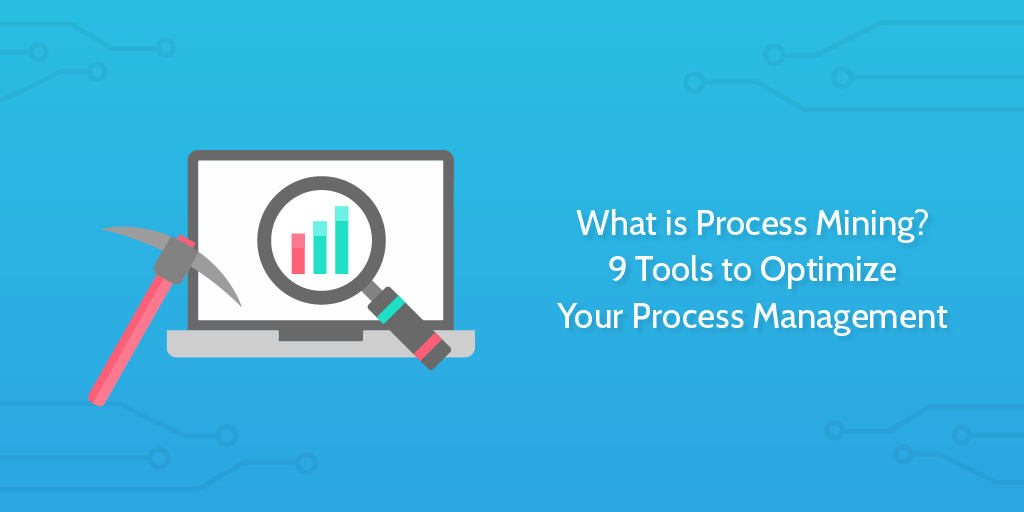
To make any process improvements, we need to be able to know how the process occurs.
If we haven’t got a clear idea of exactly what the current process is, then we have no hope of improving it.
Now, you should already be documenting workflows and processes and utilizing the ethos of business process management. Lord knows we at Process Street have harped on about it enough.
But maybe you haven’t done that yet?
This is where a technique like process mining could really prove to be useful.
Process mining is where you use software to analyze the work you and your team are doing so that you can find what order tasks are normally done in.
You can hook these bits of software up to event logs and they can pump out deep descriptions of your activity so that you have them as documented processes.
In the article linked above, you’ll find 9 tools you can use to implement process mining in your business. Most of these are Automated Business Process Discovery tools, with 6 being paid and 3 more open source tools you can use too!
These powerful process analysis tools can be a really useful aid when you’re fighting through the details of Six Sigma.
Once you have the process documented, you can also use these tools to check that work which is being done is being done the way is should be done. Bit of a mouthful.
This is called conformance checking. It’s an important component of understanding your processes, because there is no point having processes documented if no one is actually following them.
Process mining helps on both of these fronts. However, it’s worth combining process mining with other bits of software.
Process Street makes sure processes are documented in a linear fashion and does a great job of enforcing process conformance and adherence.
A tool like Draw.io can be used to create visual process maps which can communicate processes very quickly. These process maps can be really useful ways to get a solid overview of your processes.
A simple process map may just be a flow chart, or you might use industry notation like Business Process Model Notation (BPMN). You can see an example of this in the image below.
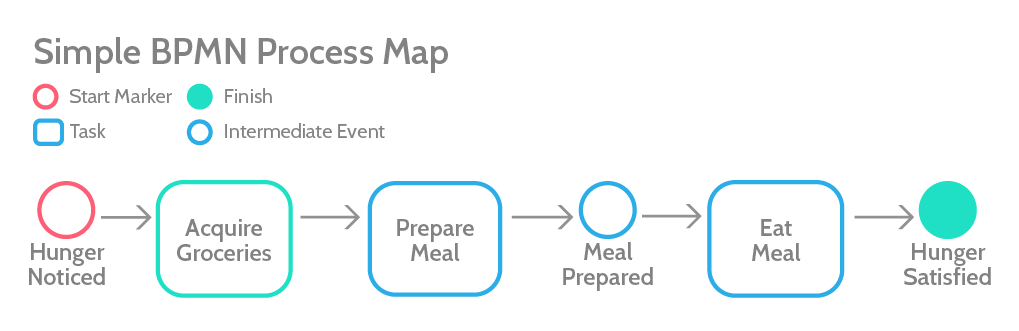
If you’re looking to create new processes then you should check out our post on DFSS – Design for Six Sigma; this walks you through creating a new process from scratch in a way which will leave it ready for further Six Sigma optimization efforts!
Make your processes flow smoothly
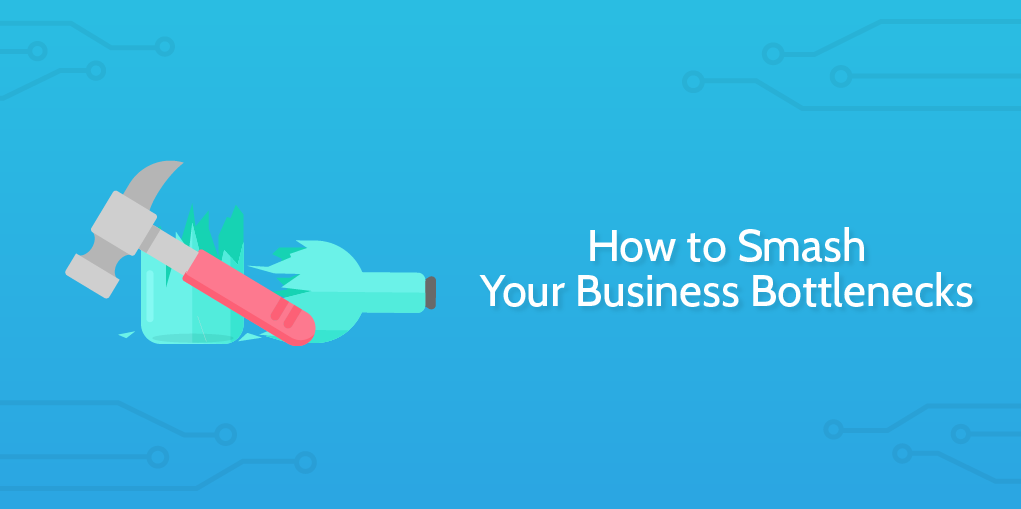
One of the core components of Six Sigma is that everything is process driven.
In this sense, you can’t just leave things to chance or ability. The process must be smooth and functional. But how do we achieve that?
Well, one of the first steps is to figure out and understand the problems.
A common kind of problem within a process is a bottleneck; where an area of the process performs below the standard of the rest, bringing all areas down to its level.
Bottlenecks are probably the clearest kind of failure to achieve a smooth process flow.
If you’ve employed a technique like process mining then you’ll likely have software which can point out most bottlenecks as part of its analysis. The Automated Business Process Discovery tools in particular tend to be able to identify and highlight bottlenecks as part of their package.
If you’re running a smaller operation, you could always utilize a technique like the 5 Whys.
The 5 Whys is simply asking why 5 times. The idea is that after 5 questions you’ve boiled down to the Root Cause: normally a process malfunction, or a lack of a process. See the example below with the example problem of: “The vehicle will not start”.
- Why? – The battery is dead. (First why)
- Why? – The alternator is not functioning. (Second why)
- Why? – The alternator belt has broken. (Third why)
- Why? – The alternator belt was well beyond its useful service life and not replaced. (Fourth why)
- Why? – The vehicle was not maintained according to the recommended service schedule. (Fifth why, a root cause)
Reduce waste and concentrate on value
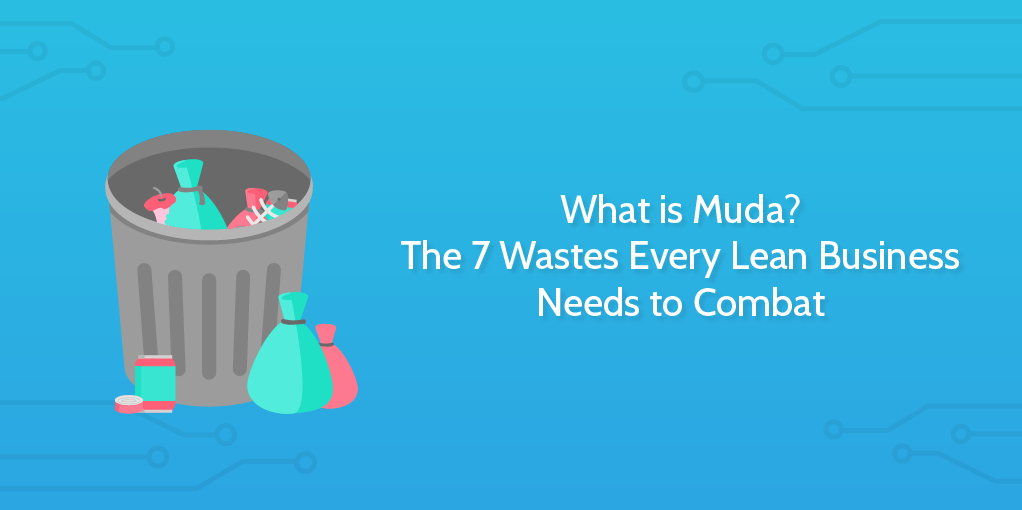
If we want to prioritize value then we need to cut out everything which doesn’t contribute value.
This means getting rid of everything which could be considered waste or wasteful.
In the Toyota Production System, waste is referred to as muda and the TPS approach to muda gives us some really easy and helpful ways to think about how waste is or can be constituted.
The 7 core mudas in the Toyota Production System are:
- Waste of overproduction (largest waste)
- Waste of time on hand (waiting)
- Waste of transportation
- Waste of processing itself
- Waste of stock at hand
- Waste of movement
- Waste of making defective products
But how do we counter these different types of waste?
Rene T. Domingo, in his paper Identifying and Eliminating The Seven Wastes or Muda for the Asian Institute of Management, presents the 5 steps he believes are necessary for eliminating waste:
- Make waste visible.
- Be conscious of the waste.
- Be accountable for the waste.
- Measure the waste.
- Eliminate or reduce the waste
In this sense, the data driven reputation of Six Sigma would be found in step number 4. To get to that point of measuring the waste, however, you need to create a culture of fighting against waste.
Once a certain category of waste has been identified, it’s possible to implement systems which can tackle that specific waste.
For example, the waste of overproduction can be managed via lean manufacturing techniques like Just In Time production.
Or, waste of processing itself could be countered by One Piece Flow assembly systems.
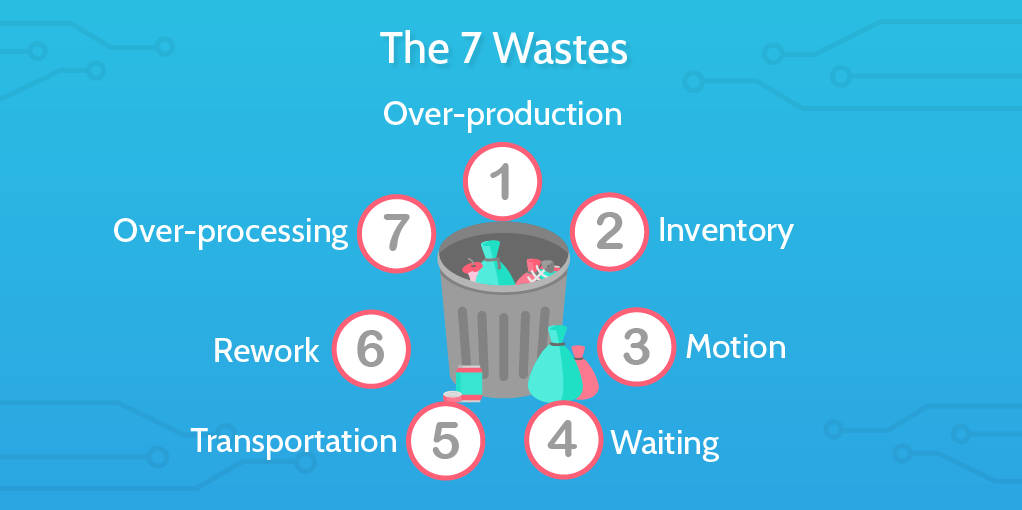
Stop defects through removing variation
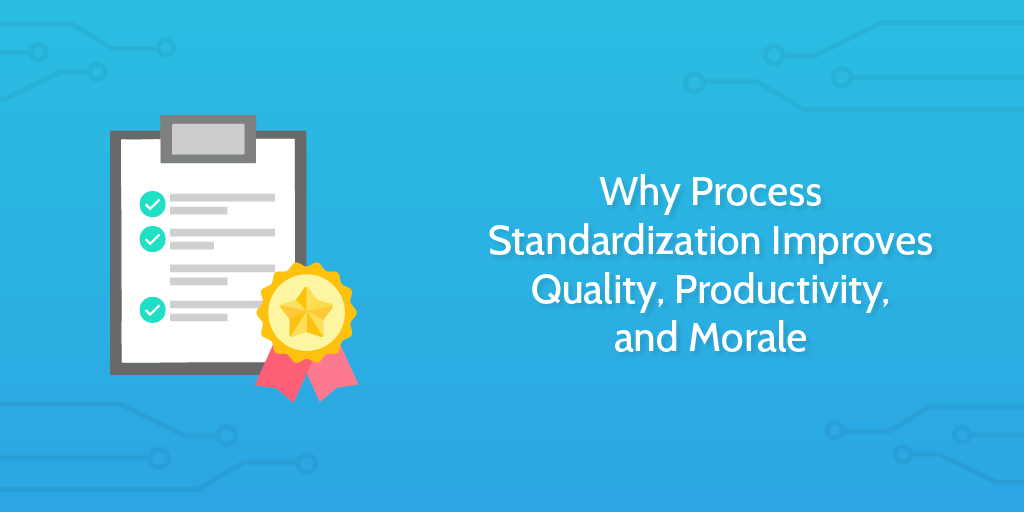
This is arguably the core of Six Sigma.
By optimizing a process and getting it to run right every time, we can massively reduce our defects.
The real key here is standardizing our processes. The more you can remove variation and have the process run at its best level every time, the more you can cut out defective output.
Standardization is one of the key things to aim for in Six Sigma when it comes to manufacturing products and dealing with your mechanical and industrial style production systems. But standardization is obviously an important goal for people working with the ethos of lean Six Sigma too.
A tool like Process Street can be used by factory floor workers, programmers, or marketing executives alike. The act of deploying checklists to standardize an approach, mandate certain activities, and provide a record of work which has been completed is something which can be used in any business or organization.
Using things like checklists to standardize actions helps to remove variance, assisting us toward our final goal.
Other features help us with optimization too:
- Stop tasks mandate certain actions and prevent people from skipping responsibilities
- Task assignments help to bring multiple people into the same process
- Conditional logic allows us to add complexity and account for variations which occur
- Template overview lets you track progress across all the checklists which have been run
It isn’t just about following processes though.
It’s easier to standardize processes which lend themselves to standard repetition.
You can see a nice example below from the film The Founder, which we featured in an article about how franchises work.
In the clip, one of the brothers is trying to find out a new process for the early McDonalds workers. Not only does he find a process which can be fast, he finds a process which can be consistently fast and lends itself to standardization.
Check out the video as it’s a great clip and only short!
Get buy-in from the team through collaboration
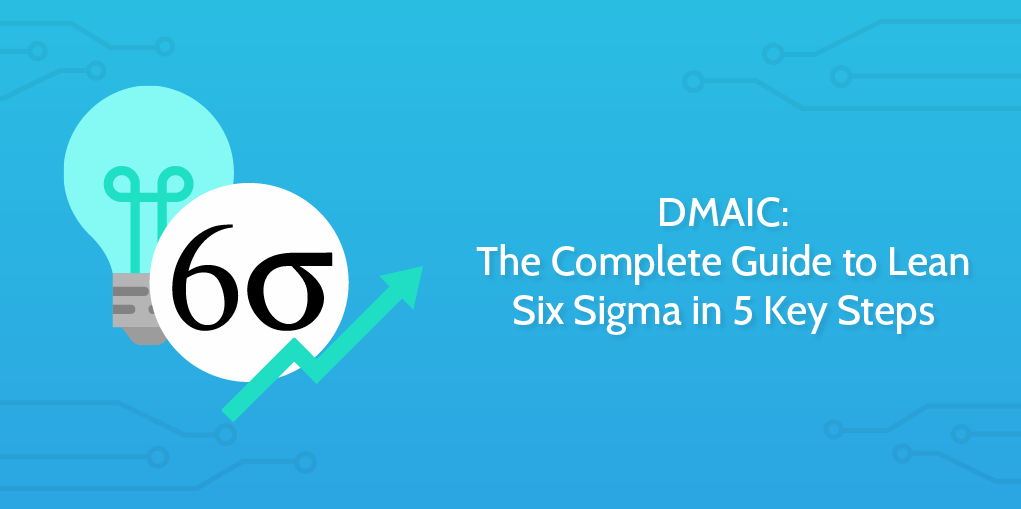
If you’ve read a lot of my previous work, you’ll already know I’m a big advocate for collaborative working.
While managers and analysts can make excellent decisions looking down on a process from above, I harbor a strong belief that the employees involved in the process on a day to day level have important insight too.
And that’s not just me saying that. It’s one of the components of the Toyota Production System.
I feel that it’s an aspect accentuated by the Toyota concept of Genchi Genbutsu; go and see. With this concept you should go to the place where improvements are to happen so that you can see the issues for yourself. This is something Toyota use for process improvement and even product design.
The point is, employees who use the process every day likely have very useful input into how a process can be improved.
Plus, I’ve chosen to use the image for the DMAIC process post in this section as that article outlines the fact that a team is required to carry out a full Six Sigma operation.
Within Six Sigma different members of the team responsible for the process improvement project are given different titles:
- Process owner
- Process champion
- Black belt
- Green belts
Kung Fu Panda aside, these team members have different responsibilities, some of which are focused around liaising with other staff or employees.
Getting other teams in the company to recognize the problem and buy-in to the solutions is a vital part of the Six Sigma team’s job. One of the best ways to get buy-in is to involve staff in the improvement process, at minimum through consultation surrounding the original process problem.
Running an organization isn’t like programming a computer. People are involved. We need to work well with these people in order for these people to work well. They are part of the process too.
Make your efforts systematic and scientific
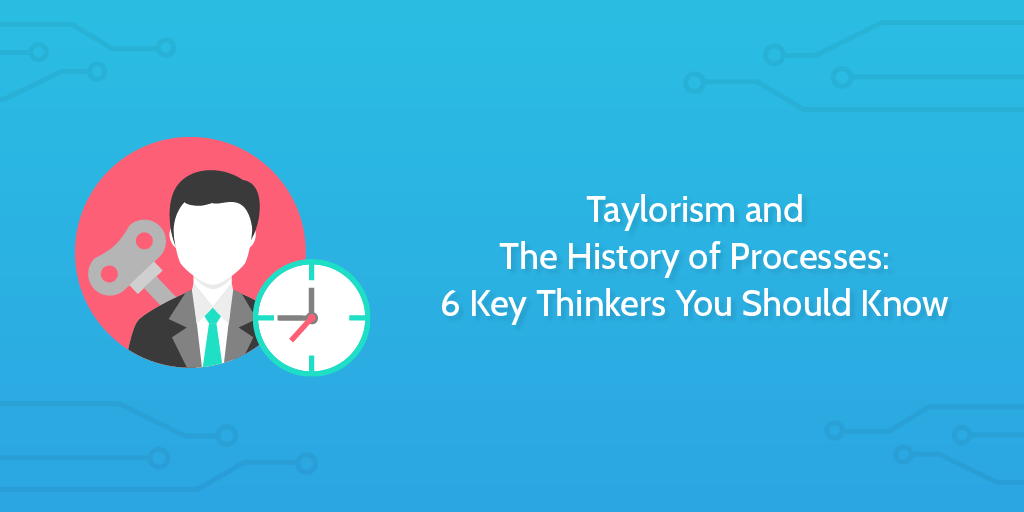
Fundamentally, the reason why Six Sigma is such a popular process management approach is that it formulates a system through which you can improve your processes.
Six Sigma has a scientific quality which resonates in the data driven world we live in. When we are capable of gathering so much data about how things operate, it seems only natural to find ways to leverage that data to create and maintain improvements.
This ethos goes all the way back to thinkers like Frederick Winslow Taylor and W. Edwards Deming who we profiled in our post on the history of processes. These were the kinds of thinkers who demanded a scientific approach to business operations.
Deming, in fact, went to Japan after the Second World War and is often credited with sparking Japan’s post-war fascination with process improvement. Concepts like the Toyota Production System are often seen to have come from this tradition of thought in Japanese production with Deming as one of the roots.
Six Sigma is most often ascribed to the engineer Bill Smith while he was working at Motorola in 1986 and it follows in the vein of these advancements.
As such, Six Sigma started out as a highly positivist quantifiable affair. For the most part it still is.
The DMAIC process is the key system within Six Sigma and looks at how you can effectively define a problem, calculate what success would be, and measure your attempts to get there.
Six Sigma is all about a systemic scientific-as-possible study of business operations.
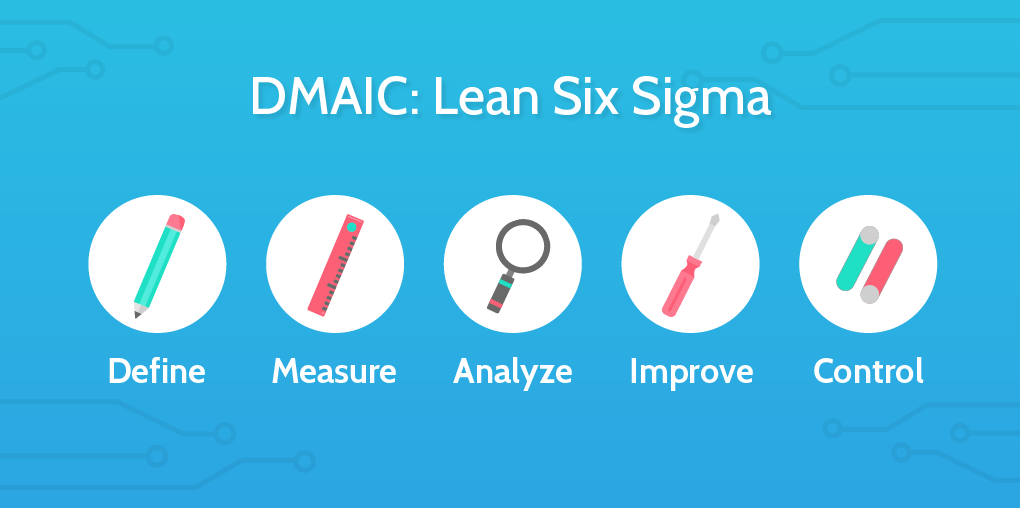
Systemize your business with these Six Sigma principles
These are the core principles and you’ll do well to attempt to implement their ethos in any business!
If you want to go further than just implementing the Six Sigma principles in your business, then check out our post on the DMAIC process for a clear step by step run through of how to approach Six Sigma techniques in your operations.
That article takes you through the 5 key steps to undertake a Six Sigma process improvement exercise within your organization. It also adds some preliminary steps and other flourishes to help keep you on track.
It gets dense at times – I’m going to be honest with you! But we all need to go in depth sometimes in order to achieve our best results.
If you want to learn more about Six Sigma and business process management in general, check out this overview article of 14 BPM and Six Sigma courses you can take to become a systems expert!
Have you used Six Sigma approaches in your business? Did you go lean? Would you have any principles you believe should be included in a list like this? Let me know in the comments below!
Adam Henshall
I manage the content for Process Street and dabble in other projects inc language exchange app Idyoma on the side. Living in Sevilla in the south of Spain, my current hobby is learning Spanish! @adam_h_h on Twitter. Subscribe to my email newsletter here on Substack: Trust The Process. Or come join the conversation on Reddit at r/ProcessManagement.