Deepwater Horizon – arguably one of the most catastrophic industrial disasters of human history, and the estimated largest marine oil spill in the history of the petroleum industry.
It also happens to be one of the most abysmal failures of quality management by any company, period.
On an otherwise unsuspecting evening of April, 2010, approximately 50 miles off the coast of Louisiana in the Gulf of Mexico, the first in a chain of quality management related failures became glaringly apparent as the emergency response protocols were enforced after an oil leak in the drilling well was discovered.
The oversights were as follows:
- Lack of proper quality assessment resulted in weak, potentially contaminated cement or “drilling mud” used in the initial failsafe failing to properly block the leak.
- Fluid pressure tests were not properly carried out and clear warnings were ignored.
- Rising oil and gas levels were not properly monitored.
- The final failsafe on the ocean floor, designed to close the leaking pipe shut, failed to close due to the conditions of the drill pipe.
The aftermath of this chain of negligence left 11 people dead, caused over 130 million gallons of oil to leak into the Atlantic Ocean, and cost over $62 billion in damages.
Not one point of failure, but four. Clearly not an anomaly, this disaster was the result of a series of systematic failures that uncover a dark truth about the reality of cost-cutting and disregard for quality control.
Considering the stakes of an operation of this magnitude – both the lives of workers and the environment at large, just how much of this disaster could have been mitigated had proper quality management policies and procedures of risk prevention and quality prioritization been enforced and followed?
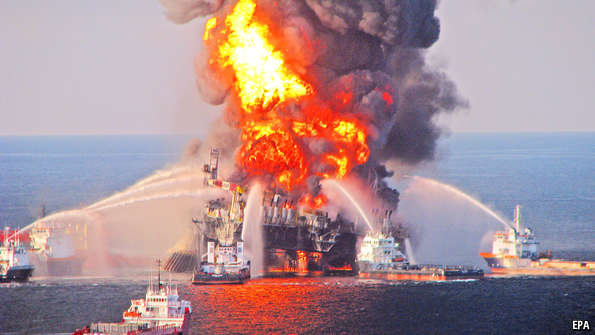
The answer to that question is by no means a clear one, but the example of Deepwater Horizon clearly highlights the utmost importance of proper design and enforcement of a quality management system.
With this article, my goal is to give you the most comprehensive guide to quality management you could ever need. Here’s a breakdown of the article structure:
- Basics of quality management
- Basics of a quality management system (QMS)
- Benefits of quality management
- Structure of a QMS
- 7 principles of quality management
- Lean Six Sigma for quality management
- DFSS / DMADV process
- DMAIC process
- Plan, Do, Study, Act (PDSA)
- Kaizen method
- Poka Yoke method
- Jidoka method
- How to implement a quality management system
- Agile ISO
- Free ISO 9000 templates
- Process standardization
- ISO 9001 certification for quality management
- Using Process Street for quality management
If you just came here for the ISO 9000 structure template, here it is:
Here’s the same template, but filled in using the example of a fictional marketing company:
You can also jump to the ISO 9000 template section to grab the rest of the templates.
What is quality management?
Quality management can be thought of as the process to make sure that products and services are working properly, and are consistent. The goal of quality management is to achieve and maintain a desired level of quality within the organization.
There are four key components that go into quality management, namely:
- Planning
- Improvement
- Control
- Assurance
Quality Planning
This is basically the process of defining standards for quality that are relevant for the product or service, and deciding how these standards will be met.
Quality Improvement
This involves the intentional tweaking of a process with the intent of improving the reliability or success rate of the outcome.
Quality Control
This can be understood as an ongoing effort to maintain the standards and integrity of any given process with regard to achieving desired outcome.
Quality Assurance
This includes any actions that are carried out in order to determine the reliability and general consistency of a particular service or product.
What is a quality management system?
What I just outlined was a more general understanding of the principles of quality management. A quality management system (QMS) is any formalized system for applying those principles in practice.
A QMS will incorporate documentation of processes, procedures, and responsibilities for achieving specific quality policies and objectives. It will also aid in coordinating tasks and processes within an organization to meet specific requirements, such as customer or regulatory needs.
Quality management systems, by design, will help to enforce principles of continuous improvement, and strive to continuously improve an organization’s effectiveness and efficiency.
ISO 9000
ISO 9000 is the name of a wide family of standards, all designed for quality management and quality assurance. The ISO 9001 standard is one of many in the 9000 family.
ISO 9001
ISO 9001:2015 is the international standard detailing guidelines and requirements for the design and implementation of a quality management system. It is probably the most well-known standard in the whole ISO 9000 family.
Sometimes the term “QMS” is used to refer to ISO 9001 and all of its related policies and procedures; however this is misleading. QMS refers to the entire quality management system, and ISO 9001 is simply a set of guidelines used to document and improve upon the wider QMS.
Benefits of quality management
Quality management, in the form of a properly enforced QMS, can help an organization to:
- Achieve higher consistency in the production process of products and services.
- Increase general product efficiency
- Reduce wastage (time, material resources, money)
- Improve customer satisfaction
- Enable businesses to market their business effectively and exploit new markets
- Onboard new employees
- Manage growth more efficiently
- Continuously improve all products, processes, and systems
Structure of a quality management system
According to various standards in the ISO 9000 family, the structure of a quality management system is made up of the following sections:
- Context of the organization
- Leadership
- Planning
- Support
- Operation
- Performance evaluation
- Improvement
Let’s go over these individually.
Context of the organization
This section states that organizations must consider both internal and external issues that might impact strategic objectives in the planning of the QMS.
The following diagram outlines each step in this section:
In this context, documenting the context of the organization involves:
- Defining the scope of the QMS
- Clearly identifying all processes and procedures
Leadership
Under the guidance of management, this section should facilitate:
- Methods for assessing effectiveness of the QMS
- Policy and goals for quality assurance
- Resource needs and allocation within the organization
- Methods of continuous improvement
- Methods to ensure that regulatory requirements are met and understood by everyone in the organization
- Policy and goals for customer satisfaction
- Roles and responsibilities for everyone in the organization
- That everyone in the organization understands their role and why the quality management system is important
It should be stressed that it is the responsibility of management to make clear that the QMS is at the core of the business and its processes, not merely a side-project.
Planning
Management will be responsible for implementing and properly maintaining the property management system. Adequate planning should be undertaken to ensure that:
- Processes, skills, and resources are adequately allocated for optimal quality assurance
- Criteria for determining quality has been suitably decided
- Each stage of design, production, inspection, and testing have been demonstrated compatible
- Standards of acceptability for all processes and product features have been clearly defined
- Specialized equipment has been properly calibrated
- Risk-based thinking as well as preventative (as opposed to reactive) strategies have been prioritized
Support
The support section involves providing all necessary infrastructure to support the proper functioning of the QMS.
That will include:
- Monetary and physical assets
- Monitoring and measuring tools
- Organizational resources
- Training or personnel
- Proper communication of quality policy and objectives
- Proper documentation of crucial QMS related information
Operation
This involves development, implementation, and control of operational processes relating to the QMS, including:
- Proper documentation of product and service requirements
- Establishment of processes to design and develop products and services
- Monitoring and controlling of external processes, products, and services
- Management and control of all production-related processes
- Management and control of processes relating to new product and service releases
- Documentation of all actions taken, including non-conforming outputs
Performance evaluation
Looking at the performance of your QMS, you must question whether the results are in line with quality policies and wider business goals.
This section includes:
- Monitoring, measurement, analysis, and evaluation of all aspects of the QMS
- Performing internal audits to assess performance and regulatory compliance
- Performing regular management reviews and clearly documenting all results
Improvement
The concept of improvement, continuous or otherwise, is a core tenet of any quality management system, and indeed the wider and more general concept of quality management in general.
There are a number of requirements in order to ensure that the QMS is continuously improving:
- Identifying all opportunities for improvement and acting on them accordingly
- Controlling process nonconformities and take measures to course-correct ASAP
- Optimizing the efficiency and effectiveness of the QMS
7 principles of quality management
The 7 principles of quality management as defined by ISO 9001:2015, are:
1. Customer focus
Any respectable organization should be prioritizing the needs and wants of their customers.
Understanding what the customer needs and being able to provide for them results in increased customer satisfaction, loyalty, and lifetime value. More efficient business processes mean higher quality, and in turn more satisfied customers.
2. Leadership
Strong leadership is essential to any good QMS. The best leaders will go beyond business performance metrics and strive to unite the workforce and shareholders together in common purpose.
Fostering company culture also means that everyone in the organization is able to fully realize their potential, and understand how they function in the larger system.
With increased involvement and higher motivation among workers, quality standards are more readily maintained – because everyone, at every step of the way within the organization – understands why they’re doing what they’re doing to achieve certain quality goals.
3. Engagement of people
Extending the principle of worker engagement outlined in section 2, high levels of staff engagement will result in higher levels of workplace happiness, increased responsibility, and employee empowerment.
When workers are involved with decision-making and feel that they are valued, they are more likely to work to their fullest potential, due to boosts in motivation and self-confidence.
With higher involvement and thus sense of individual responsibility, accountability rises and enforcement of higher standards of quality control become more feasible.
4. Process
This approach involves assessing all processes in the organization, and making sure they are efficient as well as effective.
Good processes result in improved consistency, reduced costs, less waste, and higher efficiency. Leaders in an organization will need to strictly monitor and control all inputs and outputs of internal as well as external processes.
5. Continuous improvement
Continuous improvement is a methodology that is quite self evident. It’s basically designed to make sure your processes are all as good as they can possibly be, with the aim of constantly looking for new ways to improve upon them.
This is done by assessing existing processes and determining their effectiveness, identifying problems and areas of improvement in processes, and designing innovations as well as potentially even new processes to improve overall efficiency of the organization, in relation to clearly defined business goals.
6. Evidence-based decision making
When businesses take an evidence-based approach to the decision-making process, they are more equipped to tackle new tasks and risks in order to produce desired outcome. Evidence-based decision making is about observing cause-and-effect relationships between different factors within and without a business.
7. Relationship management
Relationship management is focused on creating and maintaining beneficial relations with vendors and suppliers. Keeping a close eye on the supply chain process and optimizing where possible, as well as promoting the relationship between any interested parties and the organization in question will mean the business is more likely to achieve sustained success in areas of collaboration.
How to implement a quality management system
Assuming you’ve read everything up to this point, you should now understand what a quality management system is, as well as the basic principles and structure of a QMS.
Now, let’s take a look at implementing one, from nothing. The full outline of this process can be found here.
There are four components to implementing a QMS:
- Designing and defining your quality goals, and the processes needed to achieve them
- Deploying processes outlined in the previous step
- Measuring how the QMS is performing, in terms of its individual processes
- Reviewing the results and tweaking as needed
The basic structure of these four core stages of design, deploy, measure, and review, can be seen in a lot of the methodologies for continuous improvement throughout this article, so I’ve provided a brief outline of each of the stages.
Design
This is about setting up your goals and objectives that define quality in your organization, and then figuring out what processes are needed to achieve these goals.
It’s a good idea to define quality with the wants and needs of your customers in mind. They are, after all, the lifeblood of your business.
Deploy
Once you’ve determined the processes you need to achieve your goals, start implementing them, slowly, one-by-one.
Change management models will show you that when it comes to business, changes carry least risk when they are applied slowly, and in smaller parts.
If you can break a process down into smaller processes, do it. Keep breaking processes down into smaller sub-processes and tasks, until you can make changes that will not disrupt other, latent systems.
And of course, talk changes over with your team. Communication is key, and feedback about potential changes can help you mitigate undesirable circumstances.
Measure
You must have a system for tracking and measuring the performance of the processes that are in place within your organization. How else will you figure out what is working and what isn’t?
Review
Review your measurements and see if they align with the goals and definition of quality you initially decided on.
If they don’t you need to figure out what to tweak and change in order to improve things. Now we can start to dive into principles of continuous improvement in the context of a quality management system.
Lean Six Sigma for quality management
The image above nicely illustrates the principles of Lean and Six Sigma, and how they combine to form Lean Six Sigma.
Basically, both Lean and Six Sigma are methods of process improvement.
Lean is focused on waste management, and Six Sigma is focused on error management. Lean Six Sigma essentially tries to do both.
They are useful concepts to understand for implementing a quality management system because they help to improve processes in general, which is pretty much what quality management comes down to.
With that in mind, you can break down Lean Six Sigma into these two separate approaches:
One (DFSS / DMADV) is used when you need to improve an existing process, and the other (DMAIC) is used to create completely new processes from scratch.
Apologies in advance for these confusing acronyms, but it’s actually quite simple. Let’s look at these approaches in more detail.
Whatever approach you use, once the process or product has been developed, ideally you should aim to achieve a sigma rating of 4.5 or greater.
DFSS / DMADV
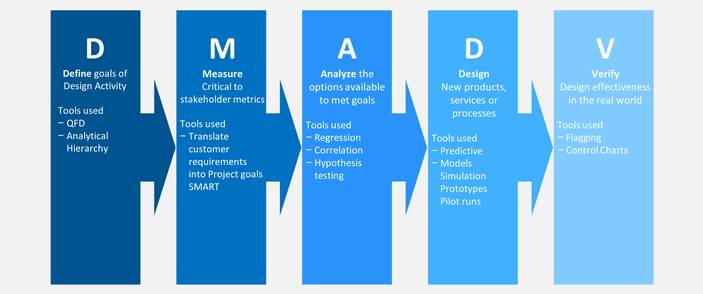
First off, DMADV and DFSS are essentially the same process. DFSS stands for “Design For Six Sigma,” and is just another name for DMADV. DMADV outlines the actual stages of the process and is a methodology for creating new processes.
Here’s a brief outline of each of the stages of DMADV.
Define
In this section you need to work out how you’re going to approach the challenge. That basically means:
- Figuring out who your customer is
- Develop problem and goal statements.
- Define what roles are going to be had across your team for this research effort.
- Define a communication plan for how this team will work together.
- Define your available resources
- Define a project plan with milestones, timeframe, budget, and resources.
- Build a process map that conveys all workflows involved in the project
See the illustrative example of a workflow diagram below:
In summary, the define stage should try to answer the question of why this process design is important for the business, as well as all relevant stakeholders. Try and make it clear why it’s important the project is done now, including consequences if action is not taken immediately.
Measure
It’s important to understand what your customers want and need. This is the purpose of the measure phase; to gather data and understand which parts of the process are crucial for providing the customer with the best possible experience, and which are merely conveniences that aren’t actually helping you give them what they really want.
“Genchi genbutsu” is a term coined by Taiichi Ohno during the development of the Toyota production system, and refers to the concept of putting yourself in the shoes of your customer to better understand their desires.
It can be an effective method to apply to the measure phase.
Other tools to help understand and measure your customer’s wants and needs include:
- Immersion into customer experiences
- Open format focus groups
- Historical data
- Current market trends analysis
- Structured interviews
- Customer surveys
Analyze
The data gathered on your customers won’t be useful until you start analyzing it.
There are many ways to read your data. One aspect of this phase involves looking at and deciding how much of your data is reliable; factors like exaggerations in reviews can impact the trustworthiness of certain data, as well as research conditions.
As such, you must be wary of putting too much faith in the face value of your data, so to speak.
Specific tools useful for clearing presenting your data for analysis include:
You could also apply a Pugh matrix to your data, which can help to determine which pieces of data are more important or “better” than others.
Here is an example of a Pugh matrix:
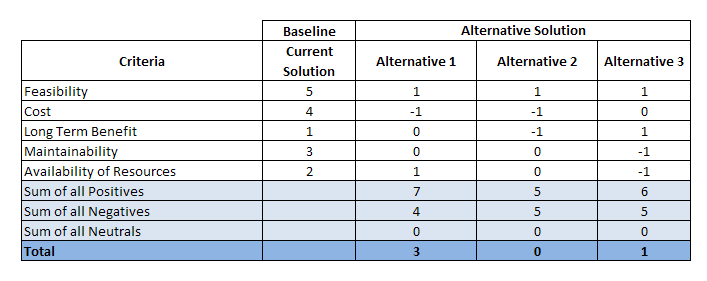
The steps for applying a Pugh matrix (as defined here) are:
- Constructing a Pugh Matrix
- Defining criteria to assess probable enhancement solutions
- Using comparative significance, allot scores for every criteria
- Determine all possible concept solution
- Weigh up how sound the potential solutions carry out on every criterion and mark scores
- Combine scores of each alternative
- Choose the best alternative with the most combined score
Design
Designing the process or product is a lot like drawing up the schematics or blueprints for a machine, but there are a great deal of ways you can approach this.
If you’re developing a product, you might design early versions with a 3D modelling tool.
If what you’re building is a process, then you might use Business Process Model Notation (BPMN) to diagram the inner-workings of the workflow.
BPMN is a kind of process mapping technique that uses visual symbols to convey complexity in the form of a flow diagram. Here’s a simple example:
We actually have a quick-start BPMN tutorial, if you want to learn more.
Of course, different stages of design (whether product or process) will require different tools. You may also want to an FMEA analysis, or a Design of Experiments (DoE).
You can use our premade FMEA template below to guide you through the process, and there’s a complete breakdown of the Design of Experiments process here in our piece on the DMAIC process.
Verify
This will involve creating and testing your product or process.
Depending on what you are trying to build, this may or may not be viable. You could, for instance, develop a prototype and analyze whether or not it meets your expectations, or consider running a pilot program or beta launch to see real responses from your user base.
Your goal with this phase is to make those final tweaks to fine-tune the product or process. If you do in fact deploy a pilot program of some sort, there are a number of business intelligence tools to aid you:
- PowerBI (comes with the Microsoft business package)
- Klipfolio (especially useful for startups or smaller businesses)
- Tableau (versatile tool that is enterprise-friendly)
Ultimately, you might consider developing a control plan. This is a detailed set of instructions to implement all of the steps that you have outlined so far in this whole DMADV process.
The control plan covers all workflows, and details why they are built the way they are. Control plans will also include intricate designs for all physical items, like products or machine equipment.
Completed control plans can then be handed off to relevant stakeholders.
DMAIC
DMAIC stands for:
- Define
- Measure
- Analyze
- Improve
- Control
It is a data-driven process that focuses on improving, optimizing, or stabilizing existing processes (as opposed to DFSS/DMADV, which is for designing new processes).
DMAIC can be summed up as a process to improve, optimize, or stabilize existing processes. That’s important – that the processes already exist.
If you’re looking for a fully fleshed-out piece on DMAIC, then we have an article on that, too.
Otherwise, here’s a concise breakdown of each of the stages of the process.
Define
This is the planning part of the process. It’s where you map out the project and clearly define your goals.
Before you can measure anything, you need to define what you’re measuring. Here are a few important Six Sigma terms:
- Unit (a singular product or process; essentially the smallest indivisible point of reference)
- Defect (a problem with the product that is caused by an issue in the process)
- Opportunity (any point in the process where there’s potential for a defect to occur)
Measure
Once you’ve defined what you’re measuring, you can gather data to understand how the product or process is performing.
Then you can start to understand how all of the different elements you defined fit together to help you make decisions:
- Defects per unit (DPU): number of defects / total number of units
- Defects per opportunity (DPO): number of defects / (number of units x number of defect opportunities per unit)
- Proportion defective (p): number of defective units / total number of units
The basic steps involved in the measure section are:
- Develop a data collection plan
- Test and validate the data collection plan
- Understand how to apply the Y=F(X) formula to your data collection plan
- Use a Sigma calculator to work out your Sigma baseline
Here’s an example of the Sigma calculator in action, with the Sigma value of 5.3 highlighted at the bottom:
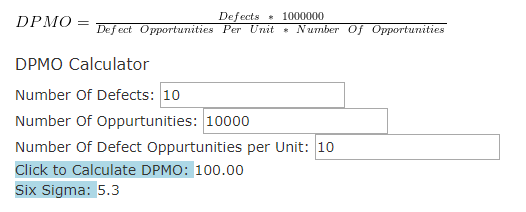
Analyze
Here you must attempt to understand where the problems in your process lie. You will need to dig into existing processes and figure out what’s causing all the problems.
Once you figure out what’s causing the problems, you’ll be ready to squash them in the next stage: Improve.
In order to determine and analyze the root causes of the problems in your processes, you could apply any number of methods, not limited to the following:
- Fishbone diagram
- BPMN map
- Pareto chart
- “5 whys” analysis
Let’s unpack the “fishbone diagram”.
A fishbone diagram organizes information into six different categories and allows you to visualize which factors in the business are contributing to which problems.
Here are the key variables, each grouped relating to different root causes of problems:
- Machine (Tools used to execute the process)
- Materia (Information and forms needed to execute the process)
- Nature (Work environment, market conditions, and regulatory issues)
- Measure (All methods of process measurement)
- Method (Procedures, hand-offs, input-output issues)
- People (Parts of the process involving people and other organizations)
And here is a neat little visualization of a fishbone diagram using the example of a company’s high turn-around time (High TAT):
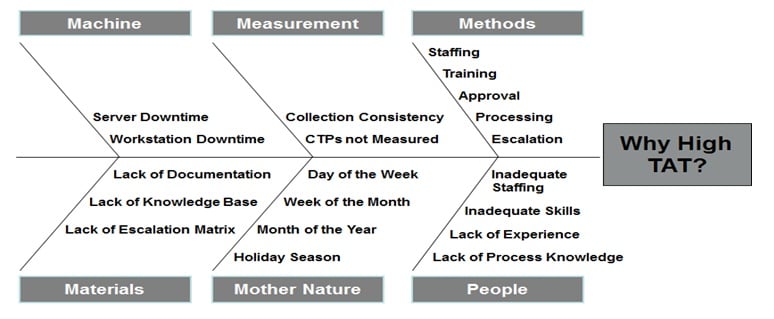
For a closer look at how to apply the other methods (“5 whys”, pareto, and BPMN) within your DMAIC process, check out the article on DMAIC I mentioned earlier.
Improve
Here you must work out how to reduce the amount of defects in the process. This involves taking advantage of all of the preparatory work you’ve done so far.
This is the first stage where we begin to see the deviation from the DMADV technique, with “improve” clearly implying that there is already a process to work with.
Here are some of the techniques you can deploy in the improve stage:
- Perform Design of Experiments (DoE)
- Implement two-level factorial design
- Develop potential solutions
- Assess failure modes of potential solutions
- Validate potential improvements with pilot studies
Control
As for control, your goal here is to plan out how to implement your solutions.
It’s about putting all of the processes in place to ensure that the solution(s) run as expected, and can be tracked and optimized over time.
Approaches to the control section:
- Standardize and document processes
- Prepare plan for implementation
- Implement statistical process control (SPC)
Plan, Do, Study, Act (PDSA)
Here’s another principle of continuous improvement that can help you with quality management.
The Plan-Do-Study-Act (PDSA) cycle, is a variant of the Plan-Do-Check-Act (PDCA) cycle. The Deming cycle is another term you may have heard used to refer to either of them.
Plan
The first step, quite simply, involves setting your goals and figuring out what processes you need to achieve them.
That sounds simple, but it could incorporate any of:
- Defining what “quality” means
- Understanding how the idea of quality relates to what your company actually does
- How your organization is structured, and how that affects quality
- Outlining a clear quality policy
- Outlining the scope of your QMS
- Identifying all processes involved
- Understanding how all of those processes work
- Understanding all risks and opportunities within the QMS
- Strategies for continuous improvement
Do
This is where you put into action everything you worked out in the previous step.
Understandably then, at this point you should already have all of your processes documented. This is to make sure you don’t introduce undocumented procedures into the QMS, because in that case it would be more difficult to understand what went wrong.
This stage also involves implementing any failsafe procedures you may have outlined in planning, in case things don’t go as planned.
Study
Processes are in place, and they are working. Now it’s time to watch them closely, and determine what is working, and what isn’t.
This is not simply a task of observing, measuring, tracking, and analyzing; you will also need to document your findings and present them in a way that clearly demonstrates to others how well your business is performing. Remember, transparency and clarity of communication are key to a successful QMS.
Act
Finally, you will need to act on the previous stage, just as “Do” acted on the plans drawn up in the initial planning stage.
The purpose of your actions here should focus on correcting mistakes that have been located in the QMS up to this point. It is also to enforce principles of continuous improvement, and so figuring out how to improve existing processes, even ones that don’t seem broken, is just as important.
More continuous improvement (CI) strategies
That’s the basics of a quality management system out of the way, along with some bare-bones strategies for designing and implementing them. We’ve even covered some of the more common methodologies for continuous improvement.
However, that is just the tip of the iceberg.
Here are some additional methods of continuous improvement:
- Kaizen (incremental improvement)
- Poka yoke (mistake proofing your processes)
- Jidoka (automatically detecting abnormalities)
Kaizen methodology
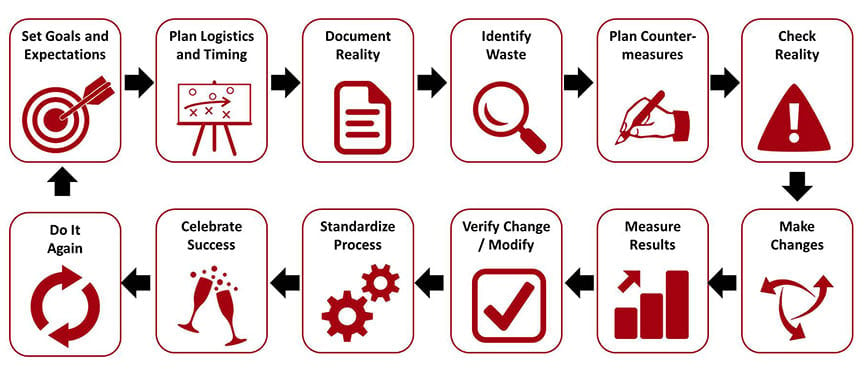
Kaizen is a Japanese term that could be translated as “change for good”, where “kai-” means “change”, and “-zen” means “good”.
In practice, the concept can be distilled into the following points:
- Improvements should be made on an incremental level
- The belief in a cumulative effect of many smaller factors contributing to a larger positive impact
By measuring and optimizing small details across all processes, we stand to improve them and in turn discover new opportunities for optimization. Cumulatively, an organization’s standard of quality will also increase.
Kaizen is ultimately a technique for continuous improvement and process innovation, and will help with marginal cost savings (in the short-term) and eliminating business bottlenecks (in the long-term).
Poka Yoke
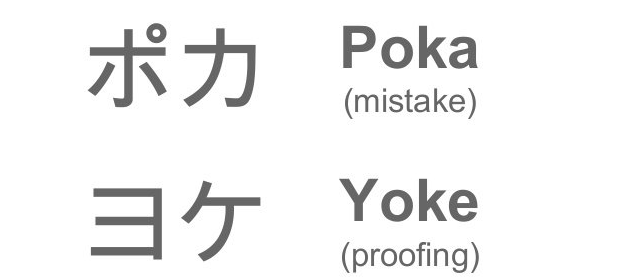
Poka (mistake) yoke (proofing) is a the idea of a step in any given process that is specifically designed to prevent errors. It is sort of like a failsafe step.
A simple example of the poka yoke principle in action is demonstrated by the fact that cars equipped with manual gearboxes still require the clutch pedal to be pressed before the car can be started. The pressing of the clutch is the poka-yoke step which stops the car from starting up and moving unintentionally.
The basic idea here is that certain steps in a process can be introduced to reduce the likelihood of mistakes.
Initially developed by Shigeo Shingo as part of the development of the Toyota production system, in the context of his broader philosophy of defect reduction as a means to improve processes.
Poka yoke recognizes that human error is always present, and instead of trying to design away these inherent vulnerabilities of process, facilitates checks and controls for those mistakes that will inevitably arise from human error.
Jidoka methodology for quality management
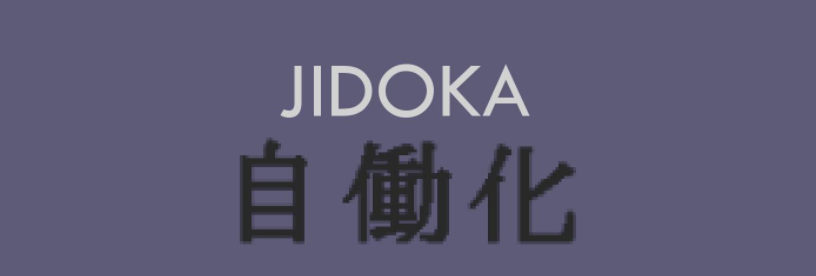
Jidoka can roughly be translated to “autonomation”, which is a portmanteau of “automation” and “autonomous”. Another way to describe the principle is “automation with a human touch”.
It is basically using automation together with the “human touch” required to identify faults and defects, and ultimately improve the process where necessary.
Together with JIT, it forms the core of the Toyota Production System. JIT can be understood as a manufacturing principle that focuses on working on a particular process or task in order to meet demand as closely as possible, with as minimal waste as possible.
Combined, JIT and jidoka help to achieve wider production goals, most notable of which is waste, or muda.
The 7 key types of muda are:
- Waste of overproduction (largest waste)
- Waste of time on hand (waiting)
- Waste of transportation
- Waste of processing itself
- Waste of stock at hand
- Waste of movement
- Waste of making defective products
By using jidoka, companies can reduce waste from defective products, inefficient processes, poorly allocated resources, logistics, and worker coordination.
Agile ISO
Standard operating procedures (SOPs) are typically very slow, boring, long-winded procedures. Recent developments in ISO standards have made it so you no longer have to rely on clunky, inefficient paper trails, and can instead trade off for specialized digital tools.
By changing the tools you use to implement SOPs and ISO standards, process iterations can be rapid, and workflows can be built from the bottom-up as well as from the top-down.
For example, in the most recent (2015) version of the ISO 9001 standard for quality management systems, there is scope for the organizations themselves to set the amount of documentation required to achieve specific business goals with the processes they use.
“This enables each individual organization to determine the correct amount of documented information needed to demonstrate the effective planning, operation and control of its processes and the implementation and continual improvement of the effectiveness of its QMS.” – From the ISO/TC 176
What’s more, these standards now make it easy for organizations to make sure their operations actually align with specific business goals, where the QMS is integrated into the business, as opposed to a kind of side-project that isn’t really part of the organization, and simply observes things as an estranged outsider.
And of course, policies and procedures can now be stored digitally, as well as on paper, which greatly streamlines pretty much all conceivable standard operating procedures.
What’s so “agile” about all of that?
Well, since it’s easier than ever to store procedures and documents on the cloud, many of the difficulties and inefficiencies of implementing SOPs and ISO standards in the past are no longer present, such as removing tedious manual tasks from workflows, and saving heaps of time and money on logistics and ridiculous time-wasting problems like misplacing paper forms.
It also means processes and procedures can be quickly and effortlessly edited, collaborated on, and shared. By making it easier to deal with problems as soon as they are identified, errors can be more readily prevented and processes improved upon. It’s “agile” because it’s quick and nimble in comparison to paper forms.
Some processes will need detailed procedures outlined with in-depth instructions, whereas others may need one but not the other. All processes are different and documentation should be a reflection of business needs, and nothing else.
This is essentially the agile vs waterfall debate, wherein some processes require careful planning from start to finish, and others can just get started and kind of learn, build, and adapt on-the-go.
Previously, ISO could only be implemented with a waterfall-style methodology. Now, with software like Process Street, it’s possible to build extensive, fully-developed process libraries, and quickly build new processes in collaboration with others, while being able to iterate upon them rapidly over time.
In other words, agile ISO is now possible.
What is needed to support Agile ISO?
In order to implement Agile ISO, you basically need software that can do the following:
- Build rich process libraries with multiple folders, subfolders, and managed permissions.
- Interact dynamically with procedures as process instances, recording information through form fields.
- Build large detailed procedures filled with work instructions, media, and reference guides.
- Quickly create new processes, assign them to individuals or teams, and collaborate on their construction and execution.
- See complete revision histories for set procedures, so you know how they were updated, when, and by whom.
- Enforce certain procedural paths through things like stop tasks and conditional logic.
- See when a process was followed, who followed it, and what progress was made on it.
- Quickly and easily update processes and immediately push the new revision live for use.
Using software with this kind of feature set allows you to reap the benefits of all of business process management, agile, and ISO standards in the form of a singular, actionable methodology for process management.
In this case, your process library is essentially acting as a complete, interactive process manual.
For example, using Process Street, the procedures take the form of checklists. You can make them as complex or simple as you need, and they can even be assigned, scheduled, or triggered automatically based on conditional logic.
That’s not even the best part. Whenever an employee needs to complete a task or follow a process, they just follow a checklist which walks them through the process, step-by-step, making it almost impossible for them to do the process incorrectly (assuming they follow the instructions, and the process is well-designed, of course).
The result is increased process adherence, improved success rates, and boosted accountability in the workplace. Unlike traditional process manuals, the processes are actually getting followed.
Agile ISO is a rather expansive topic, and this is just skimming the surface. If you want to really sink your teeth into it, check out these two posts by my colleague Adam Henshall:
- Agile ISO: A Holistic Business Process Management Framework
- Agile ISO: How to Combine Compliance with Rapid Process Improvement
ISO 9000 Templates
We have a whole bunch of checklist templates for standards in the ISO 9000 family. Feel free to grab any of them for yourself!
ISO 9000 Structure Template
Here’s an ISO 9000 Structure Template based on the ISO 9001:2015 standard:
ISO 9000 Marketing Procedures
And here’s the same template, but with all of the placeholder content filled out using the example of a fictional marketing company:
ISO 9004:2018 Self-Audit Checklist
Here’s a checklist for self-auditing your quality management system, based on the principles of the ISO 9004:2018 standard:
Standard Operating Procedure (SOP) Template Structure
Use this template to build standard operating procedures (SOPs) for whatever purpose you need:
Process standardization
If we’re talking about quality management, and more specifically implementing a quality management system, it’s important to understand the importance of process standardization.
When we talk about quality, what we’re really talking about is certain rules that have been decided, typically by you if you’re talking about quality within your organization. Assessing quality often boils down to asking whether or not there was a process, and whether or not the process was properly followed.
Thus, defining clear rules for the scope, quality, and instructions for each task in a process, and in turn all processes within an organization, is essential for building and maintaining an effective quality management system.
What is process standardization?
Short and sweet: it’s setting up rules that determine how certain tasks or sequences of tasks should be done.
You can apply standardization to any process, task, or procedure within your organization. Something as simple as answering the phone, paying your employees, recording client information, all the way to closing a huge deal or launching a new product; it’s your responsibility to determine which tasks within an organization require standardization.
What about the benefits?
The benefits of standardization
When you have a well-defined process for doing anything, there are certain benefits that are immediately apparent.
Firstly, the task usually gets done quicker. It’s also far easier to do, because all of the instructions are clearly laid out in front of whoever is doing it. Immediately that leads to time saved and reduction in potential error.
When properly utilized, standardization can and should reduce ambiguity and guesswork, boost productivity and morale, and improve success rates.
Additional benefits of standardization include:
- Improved clarity in all processes
- Higher quality services and / or products
- Increased worker productivity
- Improved workplace happiness
- Improved customer satisfaction
How Process Street can help standardize your processes
You can use Process Street to help you standardize your processes in these three key ways:
- Documented process templates
- Workflow automation
- Recurring tasks
Documented process templates
Process Street lets you build rich, highly detailed standard operating procedure documents with templates.
You can create your own, or choose from any of the hundreds of free templates in Process Street’s library. With these templates, you can standardize any number of workflow processes and save a great deal of time, money, and mental energy.
Workflow automation
Certain tasks and processes, such as client onboarding, will occur with some degree of randomness. With Process Street’s conditional logic and dynamic due dates, you can create “trigger-based workflows” to allow you to be ready to make the most of unpredictable opportunities.
Recurring tasks
Other processes will need to happen at rather predictable times. Performance reviews, maintenance, business process analysis, newsletters; these are common examples.
Process Street allows you to easily create standardized process templates and schedule them to run and recur at whatever interval spacing you need.
ISO 9001 certification for quality management
ISO 9001 is the standard dedicated to defining the inner-workings of a QMS. It outlines the criteria for defining quality management principles for customer satisfaction, leadership and management strategies, process optimization, and general methods of continuous improvement.
What is ISO 9001 certification?
ISO certification is an accolade that can be granted by verified 3rd parties that basically says “this organization has successfully implemented a quality management system based on principles of ISO 9001.
Notably, ISO 9001 is also the only standard in the 9000 family that can be certified to. This certification is not a requirement, and organizations can still implement principles of ISO 9001 informally, without getting certified.
Despite not being a requirement, there are various benefits that come with being certified to ISO 9001 standard.
Why is ISO 9001 certification useful for quality management?
Organizations with this certification can be assumed to provide products and services to a given standard.
This is attractive for clients and stakeholders, and generally beneficial to the certified organization for reasons including but not limited to those listed below.
Benefits of ISO 9001 certification
- Increased profit potential
- Greater market share
- More efficient use of resources
- Fewer errors and defects, especially recurring
- Brand image and credibility improved
- Manual work is reduced with process integration and process automation
- Organizational efficiency and effectiveness is improved by using data and evidence to inform decision making
The ISO 9001 approach looks at both the individual processes as well as how all of those processes interact with one another.
By examining the relationship between all of your business processes in the context of a QMS, you can locate areas ripe for improvement and optimization.
Check out this article if you want to see the concept of ISO 9001 certification unpacked in more detail.
ISO 9004 self audit
As well as getting certified by a registered 3rd party, you can also perform a self audit using guidelines outlined in the ISO 9004 standard.
This kind of self audit can be administered by a Certified Lead Auditor or Registrar (in an official capacity) or simply used to assess the effectiveness or your quality management system (in an unofficial capacity).
ISO 9004:2018 Self Audit Checklist
Using Process Street for quality management
Since the 2015 revision of the ISO 9001 specification, it’s been easier than ever to streamline your QMS.
With Process Street, you can remain ISO compliant, while developing high-quality, actionable, and even automated policy and procedure templates in line with your overarching quality management system.
It’s quick to learn, easy to use, and lets you keep all of your SOPs and ISO standards in one place.
Check out this video for an introduction to what Process Street can do to help you enforce your standard operating procedures for quality management:
If you’re interested in learning more ways to automate your processes, for your QMS or otherwise, you might want to take a look at these additional resources on business process automation:
- The Ultimate Guide to Business Process Automation
- The Complete Guide to Business Process Management
- Ultimate Guide to Small Business Automation with Zapier
And if you haven’t already, go ahead and sign up for a free Process Street account today! It’ll take you less than two minutes.
What tools and techniques do you use for quality management in your organization? Let us know in the comments below!
Oliver Peterson
Oliver Peterson is a content writer for Process Street with an interest in systems and processes, attempting to use them as tools for taking apart problems and gaining insight into building robust, lasting solutions.