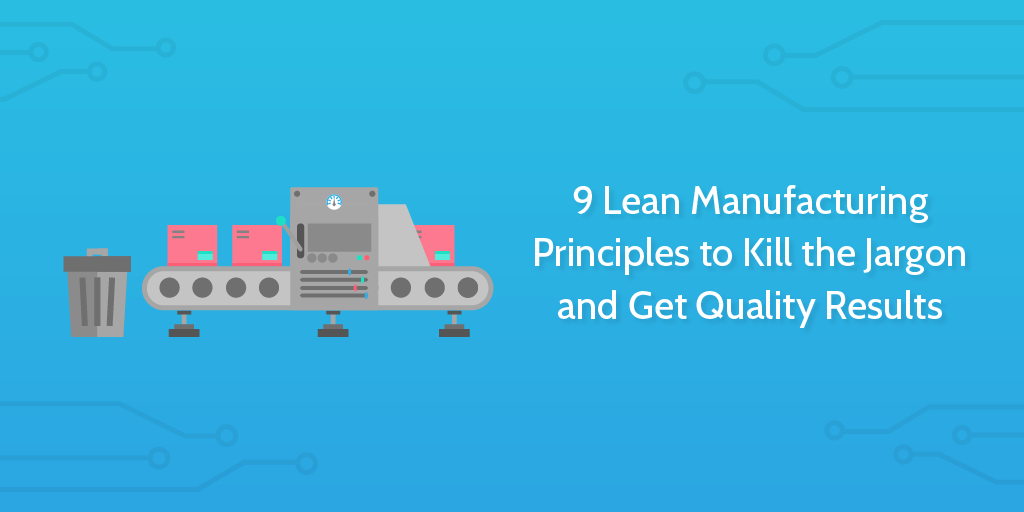
Embarking on a journey towards operational excellence? Look no further than the world of lean manufacturing principles.
In a landscape where efficiency and quality reign supreme, the principles of lean manufacturing stand as beacons of transformative change. Whether you’re a production powerhouse or a service-oriented entity, the core tenets of lean thinking have the power to revolutionize your processes, elevate your productivity, and slash wasteful practices.
In this comprehensive guide, we delve into the heart of lean manufacturing, exploring its principles, methodologies, and real-world applications. Join us as we uncover the art of streamlining operations, optimizing resources, and fostering a culture of continuous improvement.
Let’s dive into the dynamic realm of lean manufacturing and unlock the secrets to sustainable success.
- What is lean manufacturing?
- Lean manufacturing principles
- Examples of lean manufacturing principles
- The lean manufacturing cycle
What is lean manufacturing?
Lean manufacturing, often simply referred to as “Lean,” is a systematic approach to production and process management that focuses on maximizing value while minimizing waste. It originated from the Toyota Production System (TPS), developed by Toyota in the 1950s, and has since been adopted and adapted by industries around the world.
The primary goal of Lean manufacturing is to improve efficiency, reduce costs, enhance product quality, and ultimately provide greater value to customers.
At its core, Lean manufacturing is built on the principles of identifying and eliminating waste, where “waste” refers to any activity or resource that does not contribute to the creation of value for the customer. By eliminating waste, organizations can streamline their processes, improve productivity, and respond more effectively to changes in customer demand.
The key principles of Lean manufacturing include:
Value
Identify what adds value from the customer’s perspective and focus on delivering that value while eliminating activities that do not contribute to the end product.
Value stream
Map out the entire value stream for a product or service, from raw materials to the hands of the customer. This helps identify areas of waste and inefficiency.
Flow
Ensure a smooth flow of work without interruptions or delays. Minimize batch sizes and aim for continuous, one-piece flow, which reduces inventory and lead times.
Pull
Establish a “pull” system where production is driven by customer demand rather than pushing products into the market. This prevents overproduction and reduces excess inventory.
Perfection
Strive for continuous improvement (Kaizen) by constantly seeking ways to eliminate waste, improve processes, and enhance quality.
Standardization
Develop standardized work processes and procedures that are clear and consistently followed. This reduces variability and enhances predictability.
Takt time
Determine the pace of production to match the rate of customer demand, ensuring a steady and balanced workflow.
Jidoka (automation with a human touch)
Incorporate automation to catch defects early and ensure quality, while empowering employees to stop the production line when issues arise.
Heijunka (production leveling)
Smooth out production volumes to accommodate changes in demand and avoid uneven workloads that can lead to waste and inefficiency.
5S Methodology
Implement a system of five practices: Sort, Set in order, Shine, Standardize, and Sustain. This improves workplace organization, cleanliness, and efficiency.
Continuous improvement
Encourage a culture of continuous improvement where employees at all levels are empowered to identify and solve problems to enhance processes and products.
Respect for people
Value and respect employees’ contributions, involve them in decision-making, and provide opportunities for growth and development.
Lean manufacturing principles
The core principles of lean manufacturing include:
Elimination of waste
The elimination of waste is core to anything related to lean as a practice. Hence the name “lean”, as in, “with as little waste and/or excess as possible”.
To that end, one of the core lean manufacturing principles to follow is to make sure that there is as little waste as possible in and created by everything that you do. The more waste you eliminate, the more your business saves with every product it produces and every process carried out.
This includes:
- Having standing inventory (wasting space and resources)
- Making unusable by-products
- Spreading out your workstations too much, increasing the travel time between them
- Production queues backing up due to bottlenecks
- Too many workers being assigned to a limited task
- Lacking process automation where it can be used
It’s difficult to cover every case possible where waste can be reduced since there are opportunities to do so in pretty much every task undertaken. However, if you document workflows you follow for everything you do it becomes much easier to see where waste is being generated and how to eliminate it.
For example, without managing your business processes you won’t know how tasks are being performed. You might know how they should be carried out, but you won’t know what methods your team uses in practice.
If you don’t know how your tasks are carried out in practice you won’t be able to reduce waste, as you won’t even know what part of your process is causing that waste.
While it’s almost impossible to completely eliminate waste, striving to do so will cause your processes and practices to continually improve and increase your efficiency.
Simply put, if you’re not focused on reducing your waste, you’re not using lean principles.
Kaizen (continuous improvement)
Reducing waste and continuous improvement go hand-in-hand as lean manufacturing principles. By continuing to improve your business and processes you can reduce waste as much as possible by eliminating whatever bottlenecks threaten to pop up and examining which processes are inefficient.
Beyond that, continuously striving to improve is a strong approach to take with any repeated task since any improvements you make will benefit all future results.
The only way to continuously improve your practices, however, is to document and manage your processes and procedures first. As with reducing waste, this lets you see where the gaps and inefficiencies in your business are, and thus what can be improved easily (or what improvements will have the greatest effect).
Continuous process improvement doesn’t need you to start off with good processes. Heck, you could argue that starting off with bad processes means that you have more to improve and thus more to gain from continuous improvement.
Instead, focus on making sure that the processes you’ve documented are accurate. There’s no point in documenting an idealized process for how things should be done because then you have no idea where you currently stand and what improvements can be made.
It’s tough, but bite the bullet and document your processes accurately by talking to the employees involved and finding out what really happens on the front lines.
It’s better to have an accurate process that’s full of holes than an ideal model that doesn’t fit reality.
Respect your human elements (Respect for people)
When talking about lean (or manufacturing principles as a whole), having a “respect for humanity” isn’t the first thing that springs to mind.
Sure, you might value your employees and want them to be happy and engaged with their work, but making it a core principle running through every element of your business is more than most would be willing to do.
However, without respect for humanity and the people in your organization, there’s no way you’ll be able to consistently perform at a high level.
It’s also a principle which is easy in theory, as there are only a few key elements to keep in mind:
- Don’t overwork your employees
- Show them the purpose behind their work (what it achieves)
- Align that purpose with their own goals
- Maintain high accountability for success and failures
- Get to the root of a problem by talking to the employee and letting them tell you in their own words
- Ensure their tasks have as little friction as possible (nothing stopping them from working through them)
- Challenge them without demanding
- Give stability, but also variety in their tasks
In practice, each of these become much harder to manage, since you’re dealing with humans and not predictable machines. Much of your success with this principle will come down to your communication skills and the dynamics of your team and managers – as much relies on your employees getting on and supporting each other as it does on you doing the same.
In turn, if you engage your employees and show them the respect they deserve, they will produce a more consistent output which is often also of a higher quality. This is because human error is naturally reduced, as employees aren’t zoning out all of the time because they hate their tasks or their work environment.
Heijunka (level production)
Heijunka is a Japanese word which (when applied to lean manufacturing) means “leveling production”. In turn, this means that no matter what happens, your output remains the same every day.
The theory is solid – by looking at your average order amount you can keep your production consistent and avoid having to rush to meet a particular order. On days where you produce more than you sell the excess goes into a “fluctuation stock”, with the opposite happening on days where more is sold than produced.
While having a set amount of fluctuation (or “safety”) stock might seem contradictory to the idea of reducing waste such as standing inventory, this isn’t nearly as wasteful as having an entire warehouse of inventory sitting there with no idea when it can be used.
To make sure that this safety stock gets sold and doesn’t just take up space and resources, you’ll need to carefully calculate (and adjust) your production rate to match the average order amount. You can then also calculate how big your safety stock needs to be by looking at the variance in order numbers from your average.
This will no doubt take a little trial and error, but leveling out your production lets you cement the most efficient practices possible and makes your work and output easy to predict.
Heijunka is a practice best suited to manufacturing where the product’s you’re making are either complex or take a long time to create, and when the demand for your products is fairly predictable.
This is because your safety stock should allow you to always meet an order (which won’t be true if your demand spikes randomly) and having a consistent production rate is beneficial when a lot of work goes into your products.
JIT (Just In Time) production
JIT (“Just In Time”) is one of many schools of process innovation focused on reducing waste. As a manufacturing principle, it focuses on working on a task or item in order to meet demand and nothing more. Nothing is completed in excess, as that is considered waste (think standing inventory).
Unfortunately, JIT is incredibly hard to pull off and comes with so many caveats in practice that it’s difficult to even know where to start.
The ultimate goal is to have absolutely no inventory, whether that be raw resources, WIP items, or finished products. As such, applying JIT to an existing manufacturing operation requires the managers to rethink and reorganize the entire thing.
Not to mention that if you get your order predictions wrong or something happens to affect your output (en employee slows down or a machine breaks) there’s no safety net to fall back on. If you mess up, be prepared to fail to meet orders.
For this reason, JIT isn’t a must-have lean manufacturing principle. If you can achieve it then great, but otherwise consider breaking your operation into smaller sets of tasks to which JIT can be applied individually. That way you can benefit from the idea without the same level of danger associated with widespread application.
JIT doesn’t necessarily clash with Heijunka, but in most situations the method you use will depend on the complexity of your product and how predictable your demand is. Creating simple products on demand is possible because your customers won’t have to wait for very long, letting JIT flow have less of a negative in terms of how long they have to wait.
Having a highly unpredictable product demand is also more suited to JIT than Heijunka, since you can’t guarantee that any safety stock created will be used up instead of becoming surplus inventory.
One piece flow
One piece flow is the lean take on production queues and WIP (work-in-progress/process) products. By limiting your WIP to a single item you can greatly increase your efficiency and the quality associated with the end result.
Think of a production line with several workstations and a bulk order. Using one piece flow, one item is moved into the first workstation, all work there is completed, and then the product is moved to the next station. The next product is meanwhile moved to the first workstation.
One product is always being worked on at any given stage of the process, and nothing is left waiting for a station to be free. Travel times between workstations is as limited as possible (usually through an optimized floor layout) and tasks are grouped to spread the work as evenly as possible between stations.
To learn more, check out our article on the topic:
Quality built-in
The concept of having quality built into your manufacturing processes is key to running an efficient, yet successful business. There’s no good in rapidly producing cheap-to-make products if the final results are full of defects and won’t sell, after all.
Quality usually suffers as a result of either bad processes or human error, and so this lean principle is achieved by using two techniques which I’ll cover individually:
- Poka-yoke (mistake-proofing your processes)
- Jidoka (automatically detecting abnormalities)
Aside from these principles, quality is built into your processes by considering the value and product you’re providing your customers with, then making sure that your efficiency-saving methods don’t impact on the quality related to providing that value.
Poka-Yoke (mistake-proofing)
Poka-yoke (a Japanese term roughly “mistake proofing”) is one of the techniques used to build quality into lean processes, be they for manufacturing workflows or otherwise.
The idea is that every process can be engineered to inherently prevent mistakes either through re-engineering tasks to suit a standard format or by including specific measures which make sure that mistakes are caught early and corrected.
For example, in a manufacturing process, you might have a task for attaching the arms to a toy robot. Let’s say that this is done by clipping the arms onto the body while inserting a spring into the shoulder joint to allow movement. A standard process would probably just include instructions for putting the springs on the shoulder joints, then clipping the arms in place.
While serviceable, this allows for human error to occur as there’s little stopping someone from forgetting to attach a spring. The mistake is then compounded by being hard (if not impossible) to spot at a glance, and correcting it later on requires the product to be disassembled.
To save this trouble, the poka-yoke equivalent would just add an extra step to prepare two springs in advance instead of taking them straight from the stockpile.This simple change would let the worker instantly see whether they’ve inserted both springs, and thus prevent the mistake from taking place.
At the very least it would let the worker identify their mistake early on and correct it before it becomes a bigger issue.To learn more about this technique, check out our post on the topic:
Jidoka (detecting defects through automation)
Complimenting poka-yoke is jidoka – the principle that most defects can be automatically detected to completely remove human error from the equation.
Rather than making an employee check every product for defects or errors (such as a thread breaking on a loom), a machine is set up with checks built in to do the task automatically. When an error is detected, an alarm sounds to let the employees at hand know that something has gone wrong.
This human element is also why jidoka is known as “automation with a human touch”.
Examples of lean manufacturing principles
Here are some examples of how Lean manufacturing principles are applied in real-world scenarios:
Value stream mapping
In an automobile manufacturing plant, teams map out the entire production process, from sourcing raw materials to delivering finished vehicles. They identify bottlenecks, excess inventory, and non-value-added steps, leading to targeted improvements in the production flow.
Just-In-Time (JIT) production
A furniture company implements a pull-based production system. They produce furniture pieces based on actual customer orders, minimizing storage costs and reducing the need for large warehouses filled with excess inventory.
Kaizen events
A pharmaceutical company holds regular Kaizen events where cross-functional teams focus on specific problems, such as reducing changeover times on production lines. By continuously improving these processes, they increase production efficiency and reduce downtime.
5S methodology
In a semiconductor manufacturing facility, engineers implement the 5S methodology to organize their workspaces. This includes sorting out tools, setting them in an organized manner, regularly cleaning the area, establishing standard procedures, and sustaining these practices. This reduces wasted time searching for tools and increases overall productivity.
Takt time
A bakery sets its production pace according to customer demand. They adjust their baking schedule to ensure that freshly baked goods are available throughout the day, minimizing waste from unsold items and optimizing resource utilization.
Heijunka (production leveling)
An electronics manufacturer uses heijunka to balance their production line. Instead of producing large batches of one product, they produce smaller quantities of multiple products in a way that aligns with customer demand. This prevents overproduction of any specific item.
Jidoka (automation with a human touch)
An assembly line has automated sensors that detect defects in products. When a defect is detected, the production line automatically stops, and workers are notified to address the issue. This ensures that defective items are not produced in large quantities.
Standard work procedures
A clothing manufacturer defines standardized work procedures for sewing garments. Each worker follows the same steps and uses the same techniques, leading to consistent quality and reduced variations in the final products.
Respect for people
An aerospace company encourages employees to provide input on process improvements. They value employee suggestions and recognize their contributions, fostering a culture of collaboration and innovation.
Continuous improvement
A food processing plant holds regular brainstorming sessions where employees discuss potential improvements to the production process. Over time, these small changes accumulate, leading to significant gains in efficiency and quality.
The lean manufacturing cycle
The principles of lean manufacturing form a cohesive and dynamic framework known as the lean manufacturing cycle.
This cycle encapsulates a systematic approach to production, emphasizing the optimization of value delivery while minimizing waste. Rooted in the Toyota Production System’s philosophy, these principles guide organizations in streamlining processes, enhancing product quality, and cultivating a culture of continuous improvement.
By aligning their efforts with the lean manufacturing cycle, businesses can achieve operational excellence, respond more effectively to customer demands, and maintain a competitive edge in today’s dynamic and ever-evolving market landscape.